V-Core 4 Commissioning Guide
Let's get your v-core 4 moving!
This guide is meant to assist you in getting started with your freshly assembled standard V-Core 4 Kit. The entire mechanical and electronics assemblies must have been completed before. There are many ways of commissioning a 3D printer, but this guide is optimised for the V-Core 4. It aims to be the easiest, and most simple way to get your machine up and running.
(If you have not finished your mechanical assembly, click the button below)
Commissioning - ”Bring (something newly produced) into working condition.” This guide is meant to help everyone bring their newly built machine into working condition, not to fully tune and extract the full performance of the machine.
V-Core 4 mechanical assemblyAfter completing the mechanical assembly, Let's go!
The buttons below will redirect you to each of the main sections of the commissioning guide.
Configuration
Click on your machine variant to show the steps to follow.
Core XY
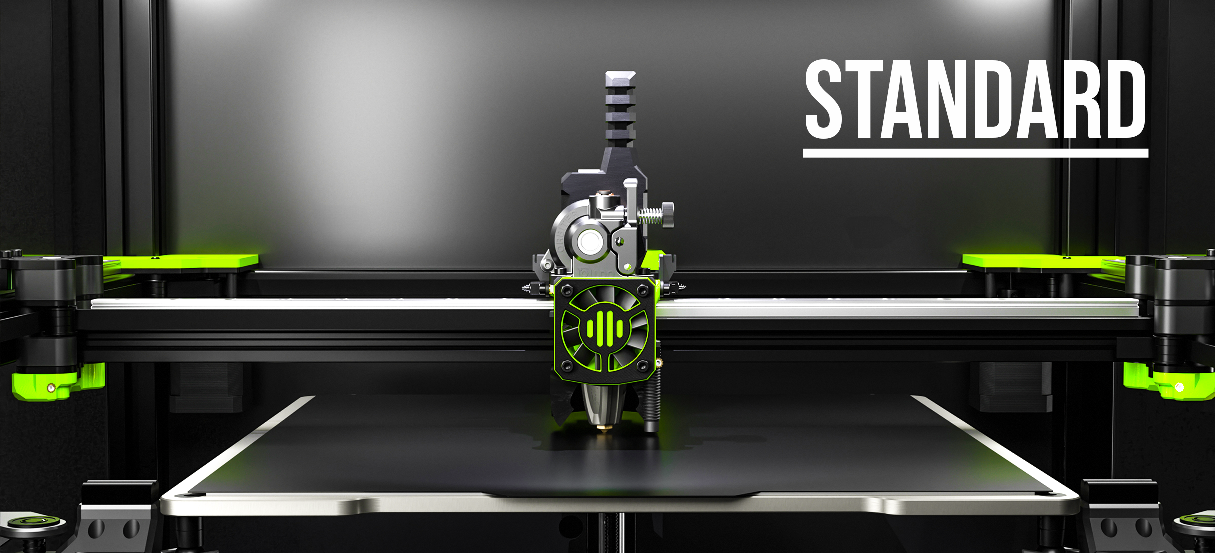
Hybrid
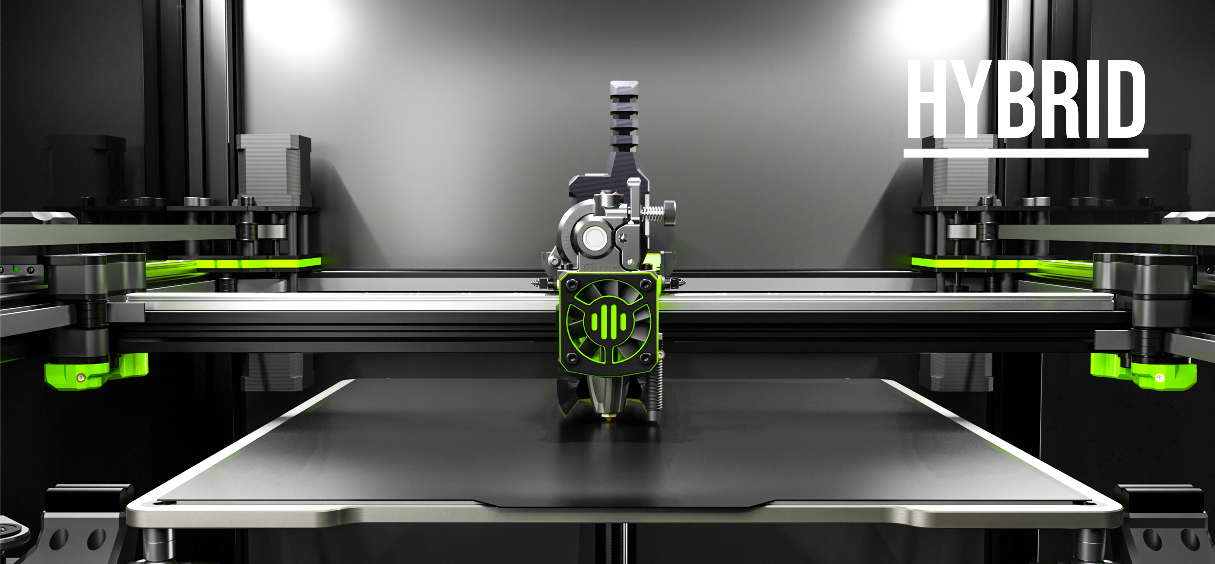
Idex
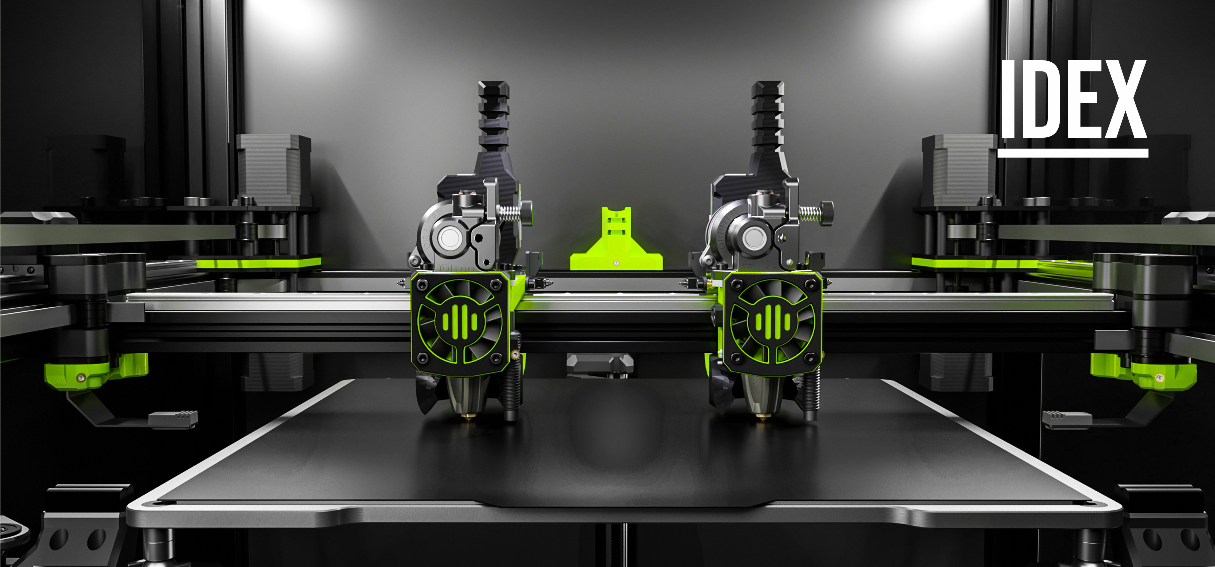
Prepare RatOs
1. Download the latest RatOS release on the button below or from GitHub (look for the RatOS-*.img.xz file under the Assets dropdown).
2. Use a tool like SDcard Formatter to prepare the SD card before flashing.
3. Write the image to a 16GB or larger SD card using Balena Etcher.
Download RatOSStep 1 - Network connectivity
1. Insert the flashed SD card into the raspberry pi and power the machine on.
2. Wait for the RatOS hotspot to appear on your control device (computer, tablet, or smartphone). this may take a few minutes as the raspberry pi is flashing the new firmware.
2.1 If the RatOS hotspot asks for a password, it is: "raspberry"
3. Connect to the hotspot and access the machine via a web browser at ratos.local.
4. On the dashboard, there will be an error, ignore it. It's only klipper complaining that there is no configuration.
4. Open the configurator (1) from the left-side menu and click on Setup Wizard (2).
5. Select your Wi-Fi network (3), enter the password (4), and click "Submit" (5).
5.1 If you wifi is not showing, click "show hidden access points" or just reebot the machine.
6. Choose your printer hostname (6), then click "Save and Connect" (7).
Some browsers may not have localhost domains acces enabled, if you have trouble connecting to "ratos.local", ensure your browser allows connection to a localhost domain.
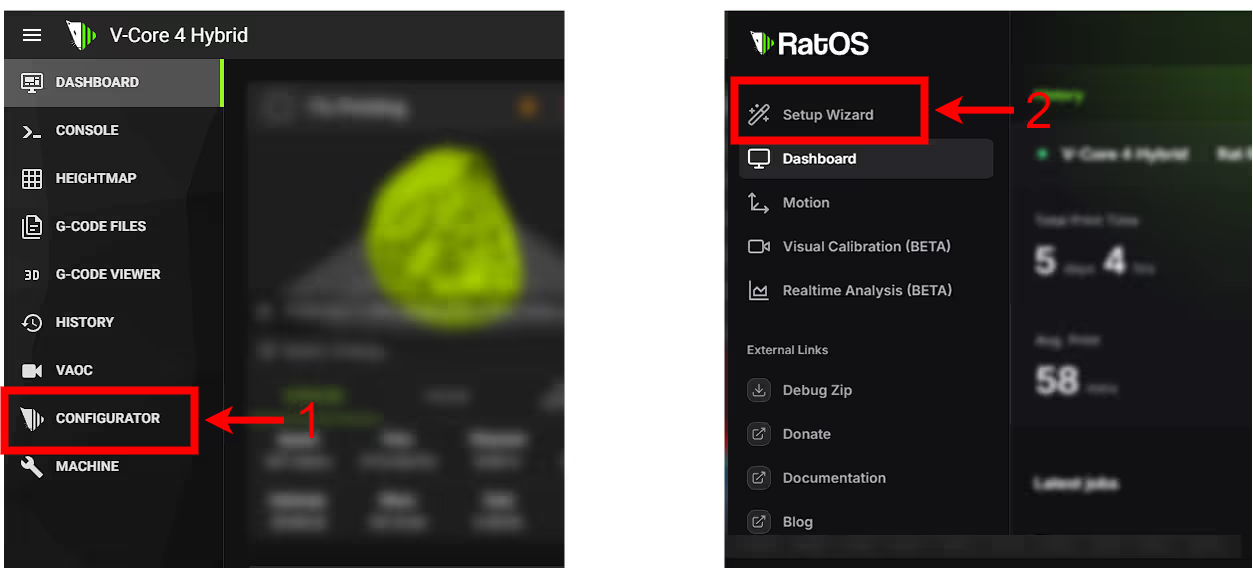
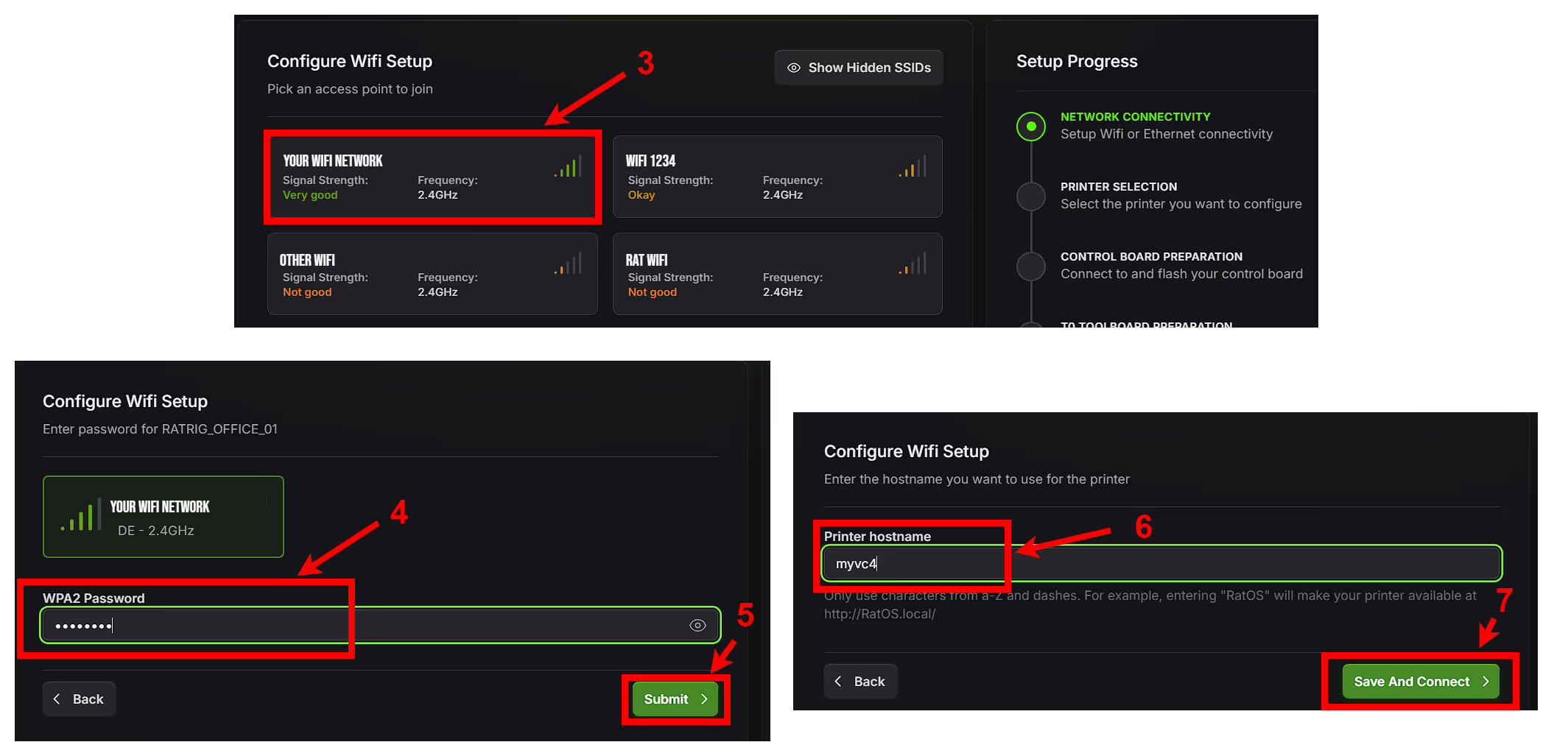
Step 2 - Updates
Follow the steps carefully; any misstep could damage the configurator and require re-flashing the Raspberry Pi.
1. The machine will reboot after the wifi setup.
2. Connect your control device (computer, tablet, or smartphone) to the same Wi-Fi network as your V-Core 4.
3. Enter the hostname (e.g., myvc4.local) in your web browser.
4. Navigate to 'Machine' (8) in the left-side menu.
5. Locate the update window and refresh it (9); options may take some time to appear.
6. Update RatOS packages by clicking the Update button (10) to prepare for third-party software changes. Wait for the machine to reboot, meaning the instalation was successful. Refresh the webpage (press f5)
7. Update the 'RatOS-Configurator' packages (11). Wait for the machine to reboot, meaning the instalation was successful. Refresh the webpage (press f5)
8. Click 'Update All Components' (12) at the bottom of the updater panel. Wait for the machine to reboot, meaning the instalation was successful. Refresh the webpage (press f5)
If any of the packages appear "invalid" just refresh the browser page, it may be loading.

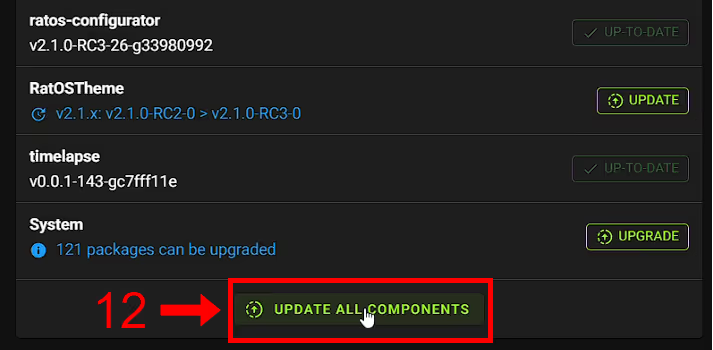
INITIAL Configuration for coreXY
This chapter is specifically intended for the Core XY configuration.
Step 1 - Printer selection
1. Open the configurator (1) from the left-side menu.
2. Go to the Setup Wizard (2).
3. In the Printer Selection menu (3), choose the Core XY (4) variant that matches your machine's size.
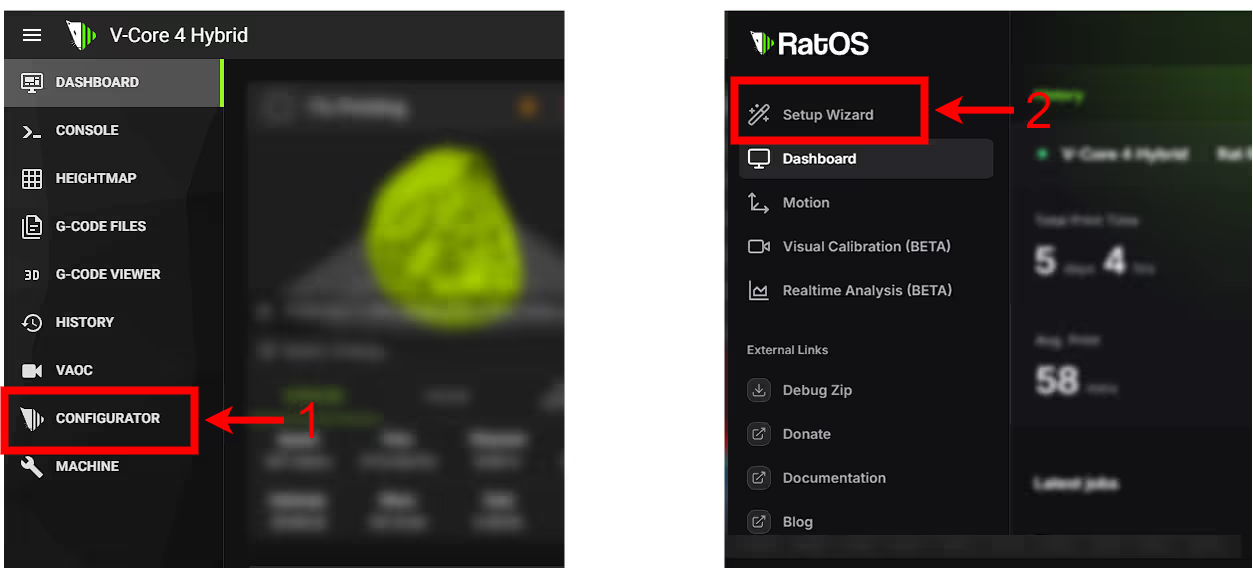
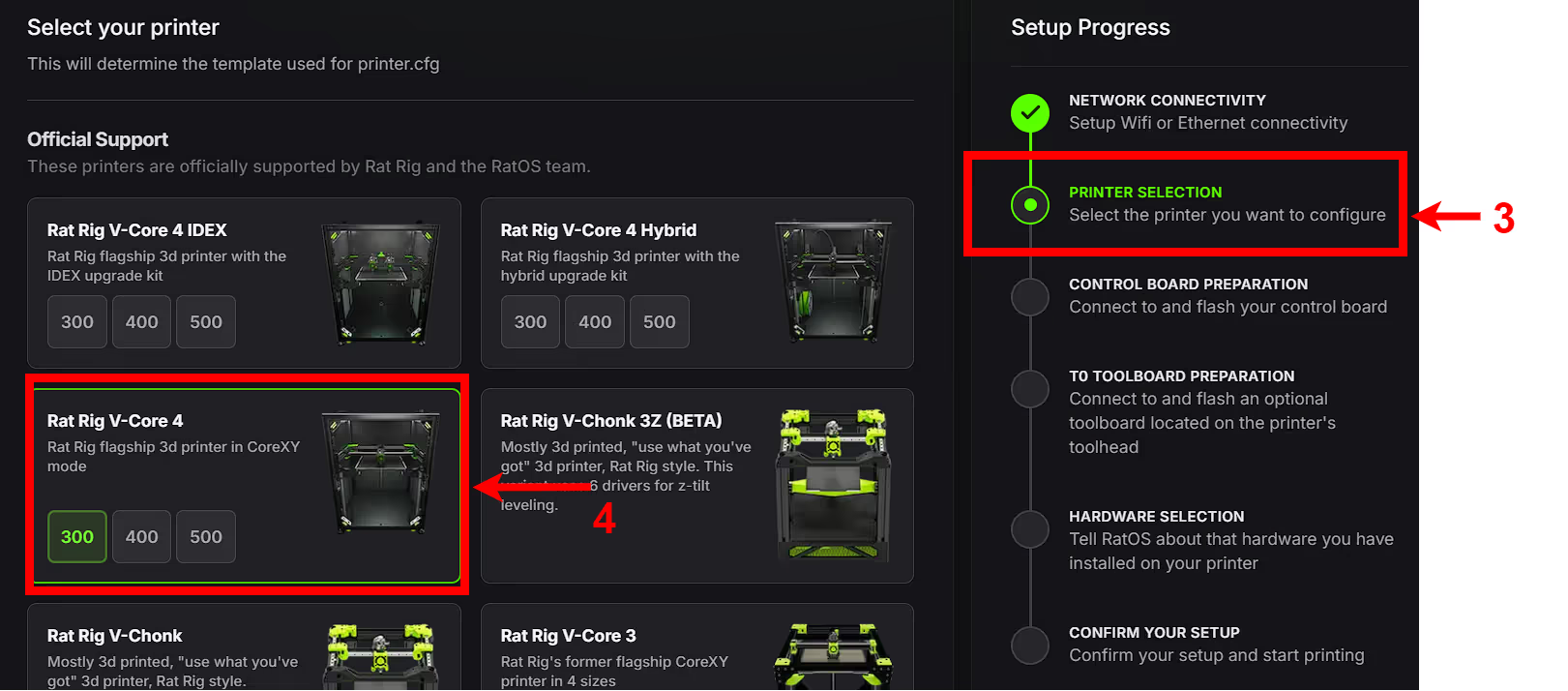
Follow the rest of the configurator to choose and flash your controller and toolboard, as well as select the appropriate hardware. During the configurator process, the standard V-Core 4 components are pre-selected. Unless your machine is not a standard kit, you should not need to change any parameters.
Sanity checks
Click on your machine variant to show the steps to follow.
Core XY
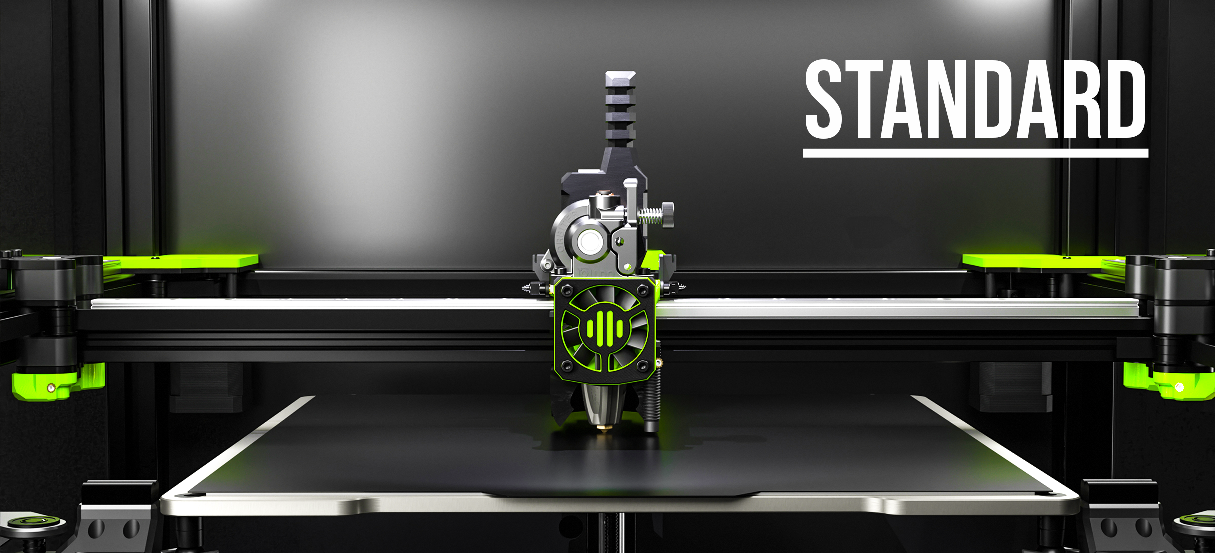
Hybrid
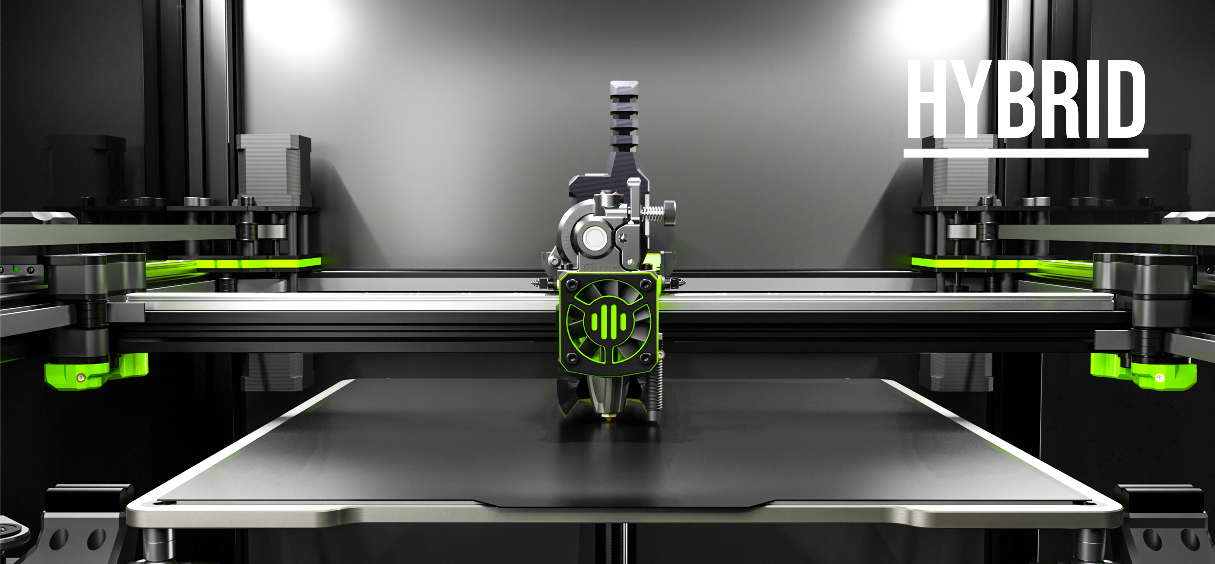
Idex
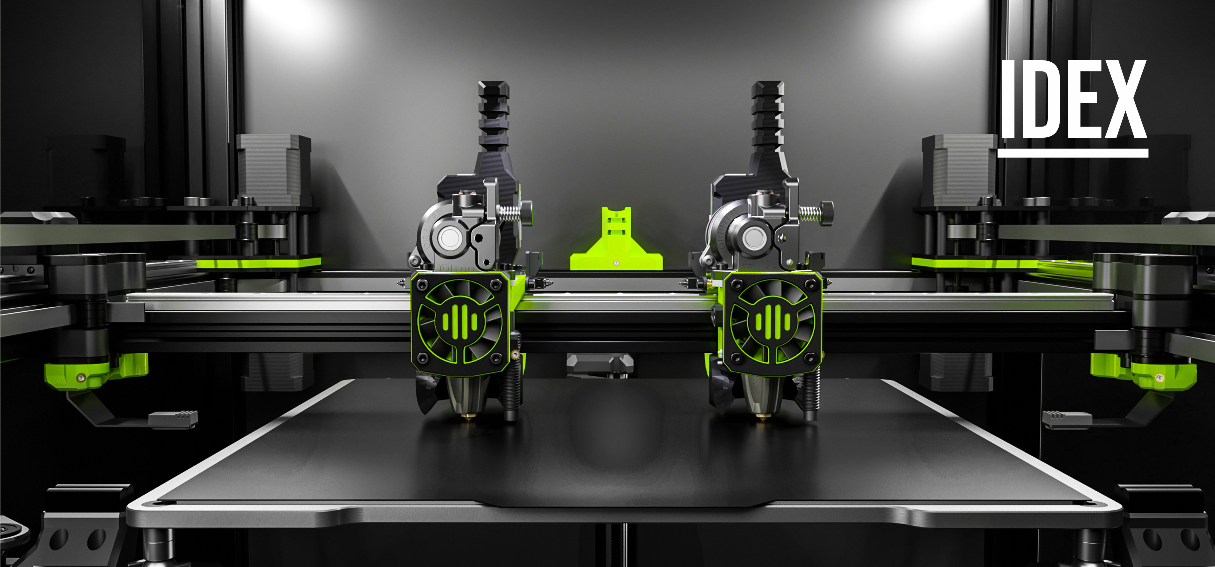
sanity checks - Core XY + hybrid
sanity checks - IDEX
Before getting started with your journey, it’s important to get familiarized with some terms:
T0 - Toolhead
X-axis - left to right direction
Y-axis - front to back direction
stepper_X - Left Stepper [L]
stepper_Y- Right stepper [R]
Please note: At this point the hybrid steppers will be ignored as the top Y belts should only be installed later in the guide.
X-axis direction (Core XY + hybrid)
1. Run the following command in your console:
M18
2. Move the toolhead manually to the middle of the build plate.
3. Run the following command in your console:SET_CENTER_KINEMATIC_POSITION
4. Use the mainsail buttons to move the toolhead 10mm to the left and right, ensuring it is moving in the right direction.
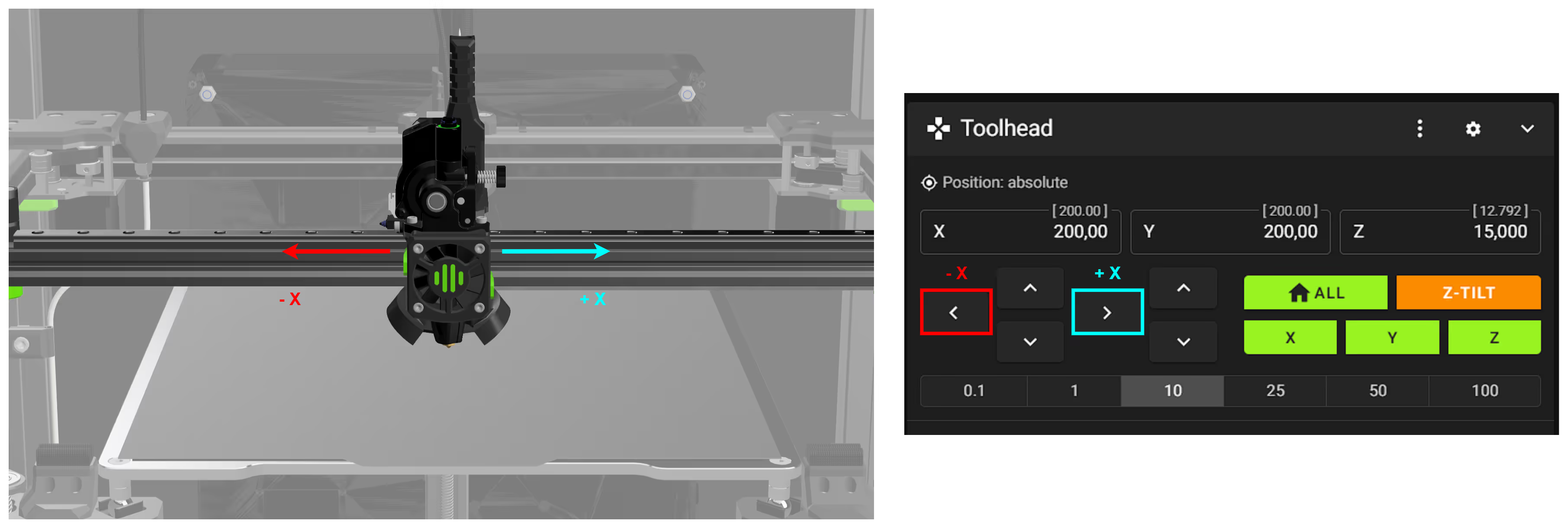
5. If the X-axis is moving in the expected direction, restart klipper and you are done, please proceed to the next sanity check.
5.1 If the toolhead moved but in the wrong direction. Navigate to the printer.cfg file and locate the [stepper_x] section. You need to invert the direction pin, by adding or removing "!" in front of the "dir" pin label, as shown below.
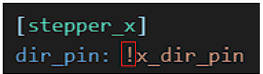
🛈 The toolhead moved in the wrong direction. HELP
6. Click "SAVE & RESTART" at the top right of the print.cfg page.
7. Repeat steps 1 to 4 to ensure the toolhead is moving in the right X direction.
Y -axis direction (Core XY + hybrid)
1. Run the following command in your console:
M18
2. Move the toolhead manually to the middle of the build plate.
3. Run the following command in your console: SET_CENTER_KINEMATIC_POSITION
4. Use the mainsail buttons to move the toolhead 10mm to the front and back, ensuring it is moving in the right direction.
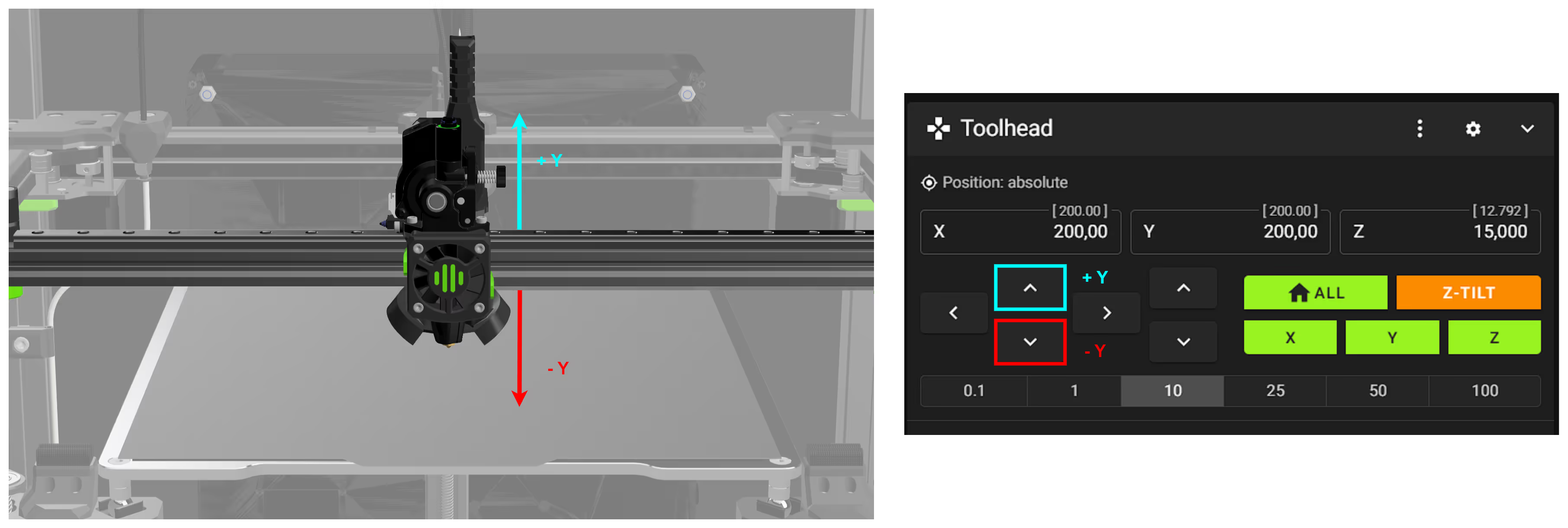
5. If the Y-axis is moving in the expected direction, restart klipper and you are done, please proceed to the next sanity check.
5.1 If the toolhead moved but in the wrong direction. Navigate to the printer.cfg file and locate the [stepper_Y] section or [stepper_X1] section if you are building an hybrid machine.
You need to invert the direction pin, by adding or removing ! in front of the "dir" pin label, as shown below.
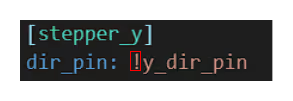
🛈 The toolhead moved in the wrong direction. HELP
6. Click "SAVE & RESTART" at the top right of the print.cfg page.
7. Repeat steps 1 to 4 to ensure the toolhead is moving in the right Y direction.
Z Stepper motor directions
1. Run the following command in your console:
M18
2. Lower the Z arms by 10 - 20mm by hand, rotating the lead screws slowly.
3. Run the following command in your console:
STEPPER_BUZZ STEPPER=stepper_z
4. Observe which lead screw moves after running the command.
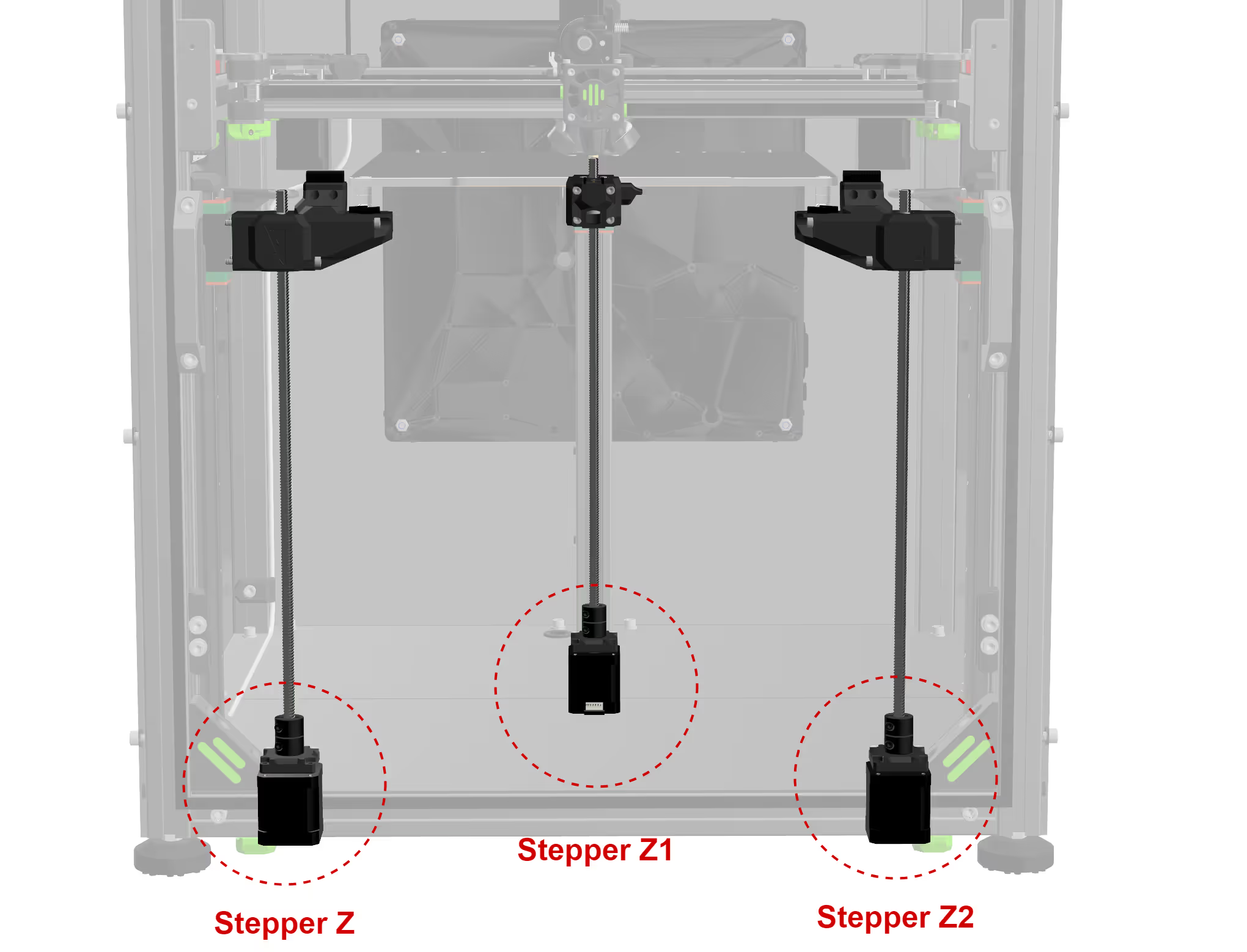
5. Only the Z stepper motor should move. If any other stepper motor moves, please note which one it is. After mapping the tree, we will swap the stepper connectors on the Octopus board accordingly.
6. Run the following command in your console and take note of which Z stepper moved. Only Stepper Z1 should move.
STEPPER_BUZZ STEPPER=stepper_z1
7. Run the following command in your console and take note of which Z stepper moved. Only Stepper Z2 should move.
STEPPER_BUZZ STEPPER=stepper_z2
8. If the correct Z stepper motor moves as commanded, , please proceed to the next sanity check, as your Z-axis is ready for action. If not, refer to the notes you took earlier and swap the connectors on the Octopus board accordingly. Click here to view the Z stepper wiring diagram.
9. Run the following command in your console:
M18
10. Lower the Z arms by 10 - 20mm by hand, rotating the lead screws slowly.
11. Use the mainsail buttons to move the bed 10mm up and down.
Carefully observe the movement of each Z arm. If any of them is moving in the wrong direction, you will need to remove the "!" before the direction pin in the printer.cfg file, as the picture below shows:
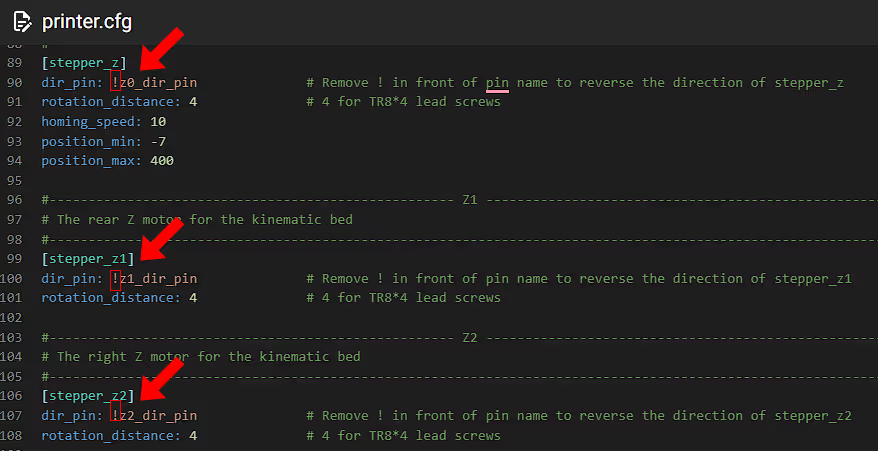
Endstops check (Core XY + hybrid)
1. Run the following command in your console:
M18
2. Move the toolhead (or toolheads in case of the idex) to the middle of the build plate by hand.
3. Go to the machine tab, find the endstops box at the lower right of the window. Hit the refresh button on the right and check if all endstops show as OPEN.
4. Manually press the endstops while hitting the refresh button, they should show TRIGGERED when pressed while refreshing. If an endstop doesn’t behave properly, it could mean a wiring problem. (Ignore the endstop Z as it represents the beacon)
PRO TIP: If the machine is positioned far from your computer, manually move the toolhead until it contacts the endstop to trigger it.
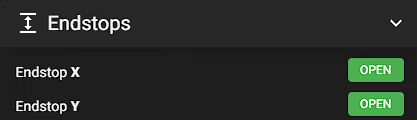
Home sequence
Provided that the machine has successfully passed all sanity checks, there should be no reason for the homing sequence to fail. As a standard precaution, it is recommended to keep your finger positioned above the 'Emergency Stop' button to quickly address any unexpected behavior during the process.

1. Run the following command:
BEACON_INITIAL_CALIBRATION
The machine will home all axis and prepare the beacon. It will home your printer and run the calibration fully
automated.
This command can throw a tolerance error, in this case just repeat it until the command gets successfully completed. For safety and peace of mind, the LED will turn on as soon as the contact system determines it has a strong enough signal for detection. It should normally turn on up to 5-10mm in advance of the metal target, allowing enough time to manually e-stop the machine if necessary.
Build plate peparation
Note: The bed heater and surface magnetic pad should not have been installed before this chapter. In the following steps, we will verify whether the bed plate is ready to proceed.
1. It's normal to have the bed tilted after assembly. Insert "M18" on the Console, this will disable the stepper motors.
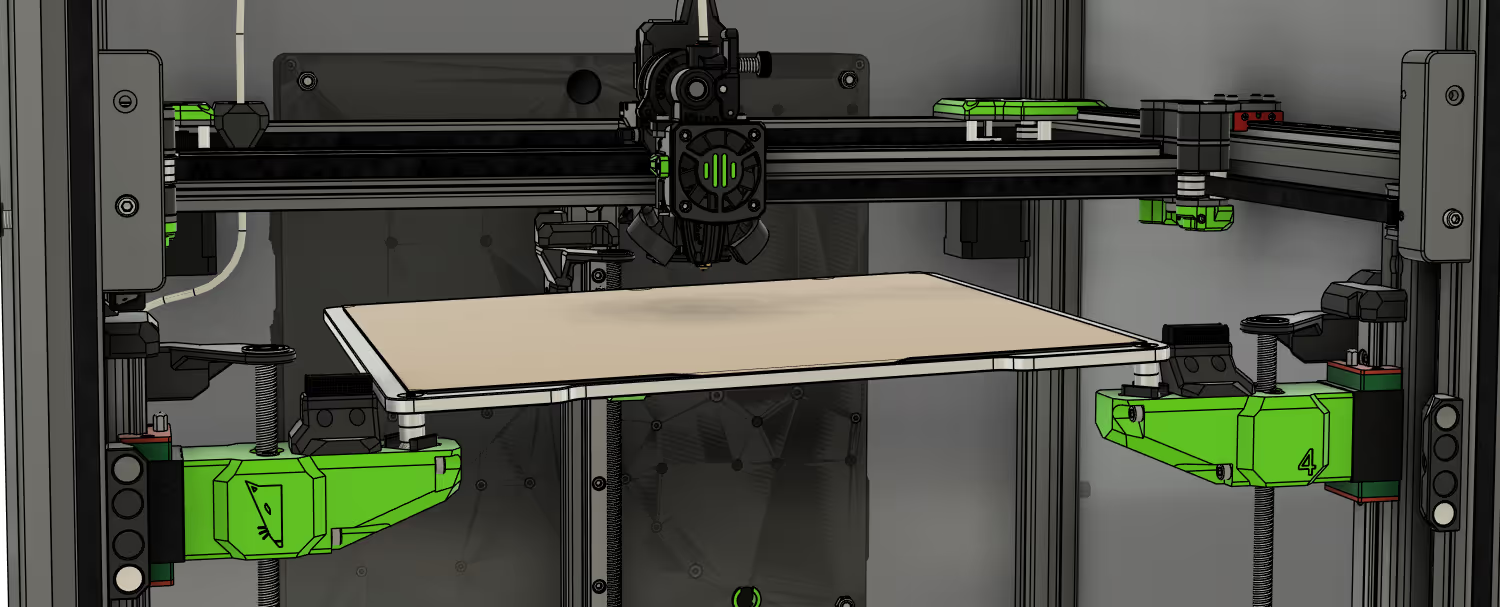
2. Manually adjust each lead screw by rotating it to achieve a roughly leveled bed. Precision is not required at this stage, as the machine will refine the leveling process later.
3. Move the toolhead to each designated Z position and make the necessary adjustments to ensure the nozzle is approximately 5mm from the bed. You may use the beacon's red light as a reference, adjusting until the light activates.
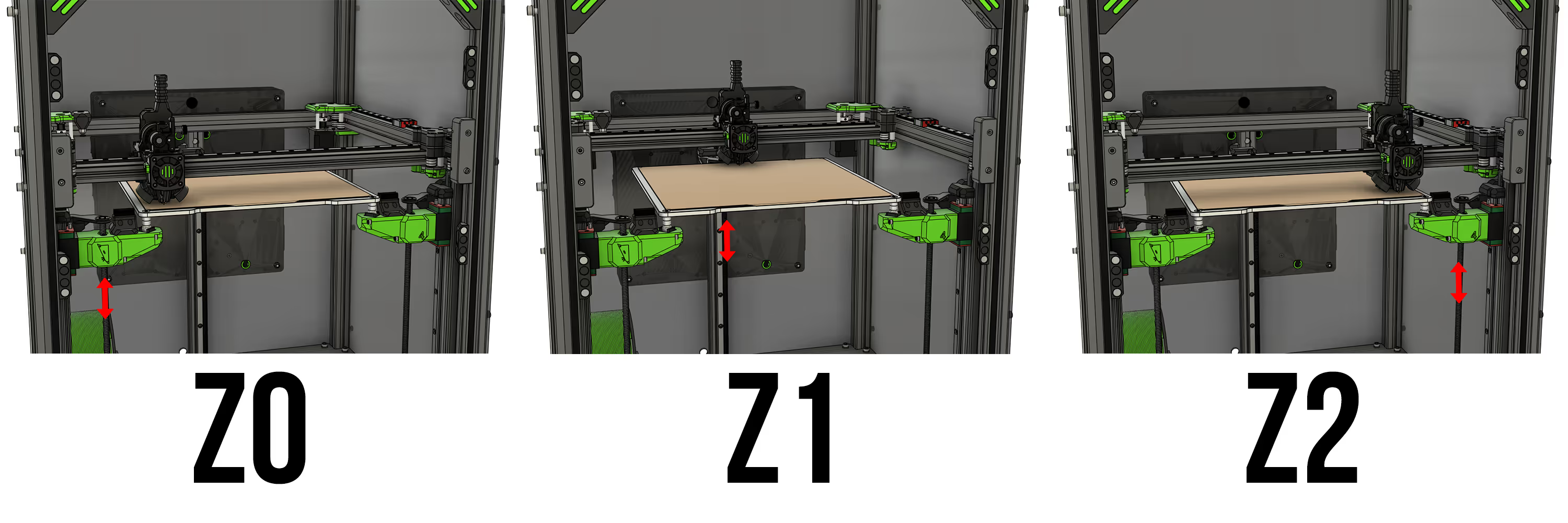
4. Now Home the machine and perform a Z-Tilt calibration, this can be found on the dashboard page.
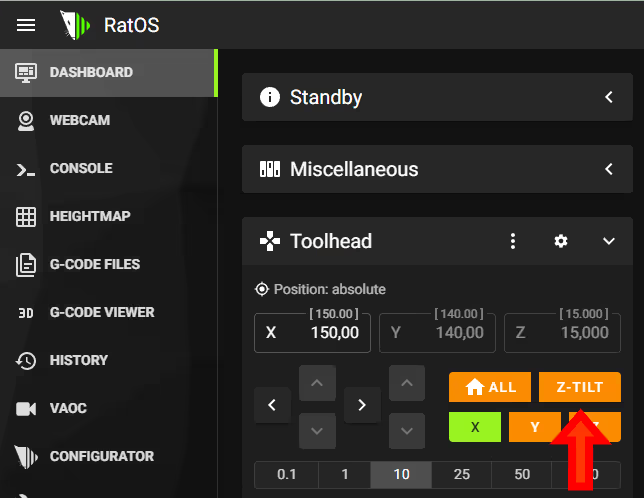
5. Proceede by clicking on the home icon inside the "HeightMap" tab. Once the printer has homed, click calibration and provide a name for this mesh as shown. RatOS will then create an initial bed mesh.
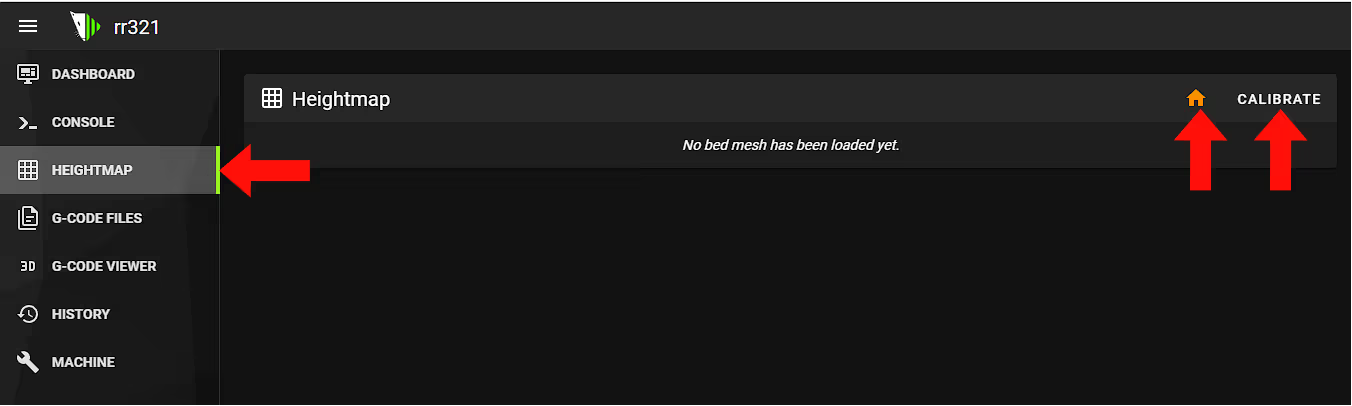
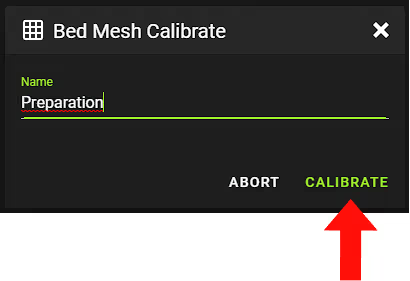
6. Inspect your mesh, to get a realistic analysis please check the “scale gradient” and slide the “scale Z-max” all the way to the right. If your mesh looks flat like the image below, this chapter is compete!
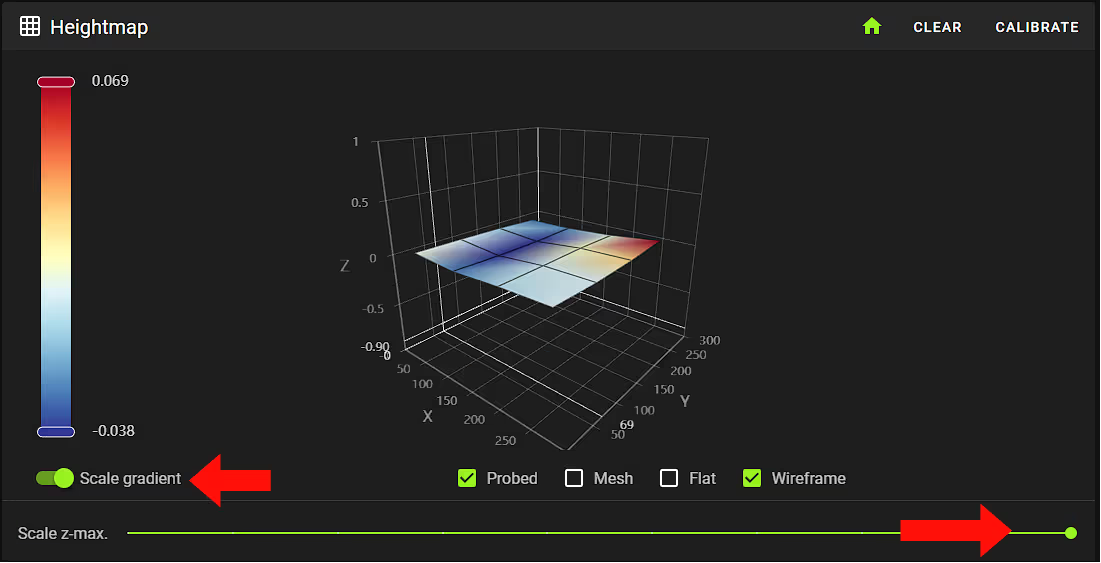
7. If your bed mesh is not flat, and appears tilted or twisted (similar to the image below), you will need to verify the alignment and squareness of your frame.
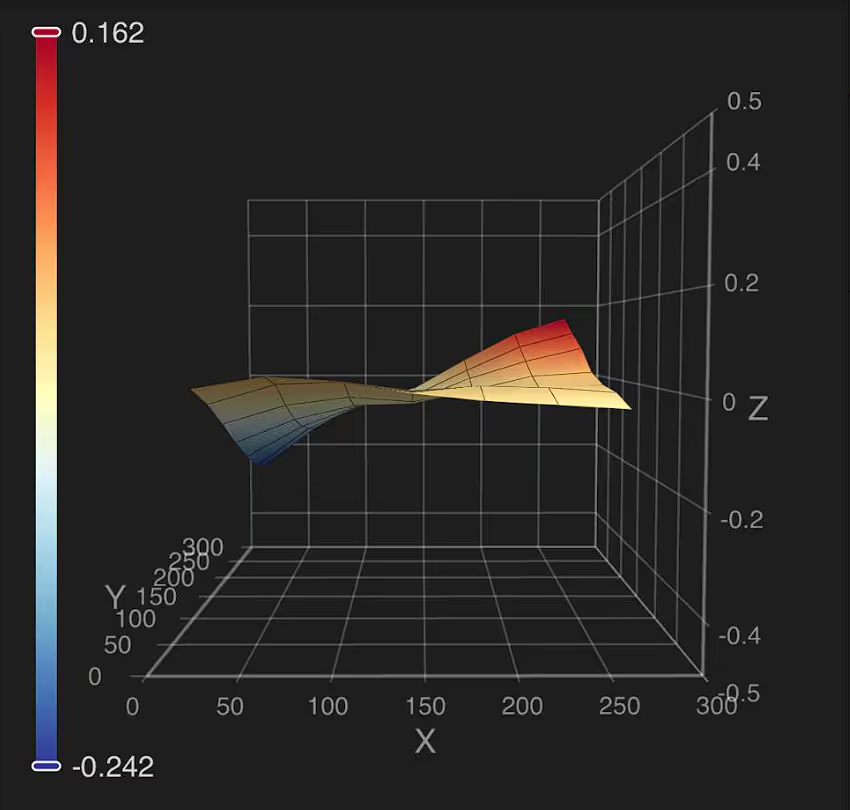
8. The image below illustrates a bed mesh with a twist. Twisted meshes are a symptom of a non-squared frame. You will observe a peak or a depression on point C or D,
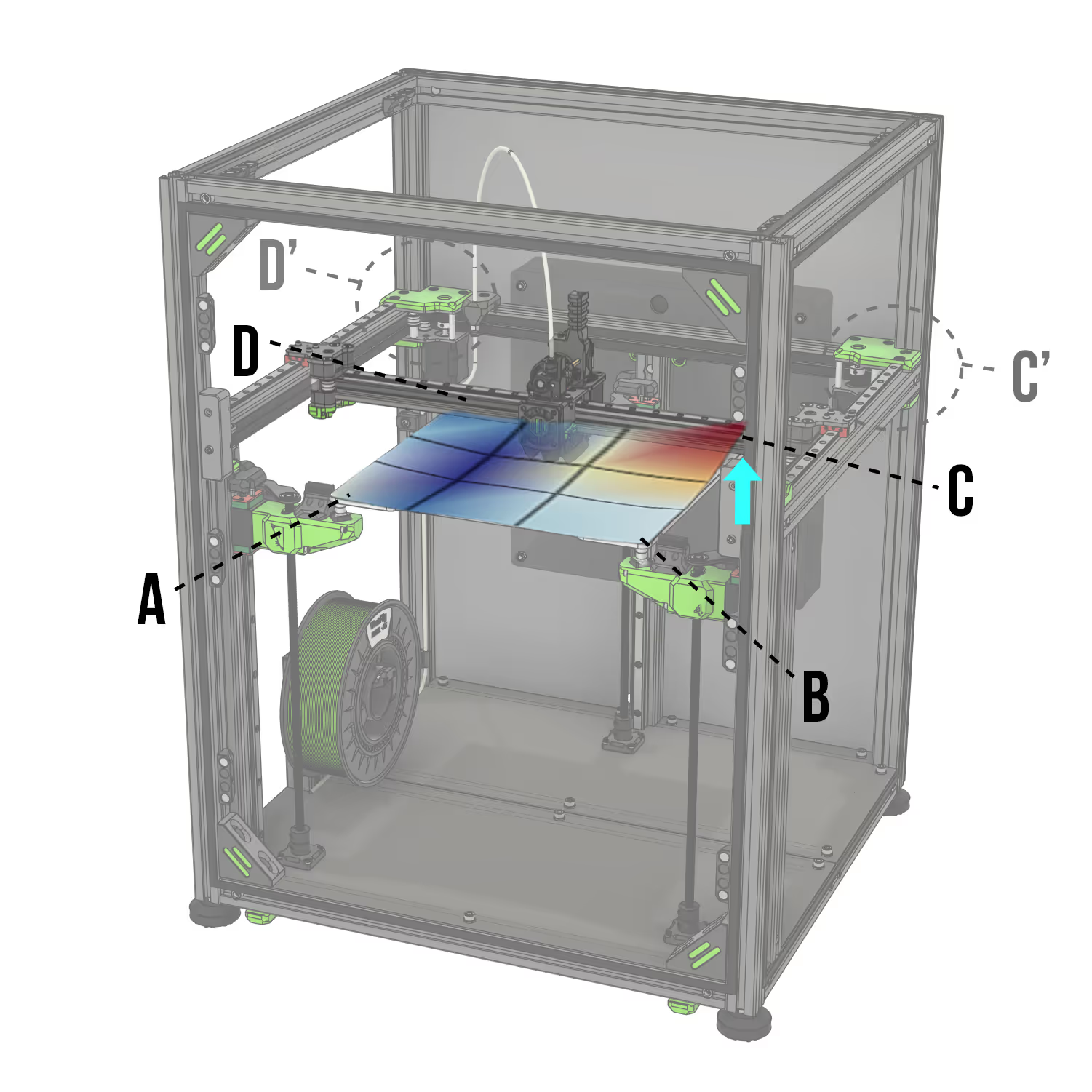
9. Identify the peak in height, indicated by the blue arrow in the bed mesh.
10. Adjust point C by loosening the highlighted quick connectors. (only C' and D' can be adjusted. Do not attempt to adjust A or B)
11. Gently tap the bottom extrusion to lower the peak.
12. Re-tighten the quick connectors and perfome a Z-Tilt calibration.
13. Run another bed mesh scan to check if the peak is resolved. If there is a depression instead of a peak, push the extrusion downward instead.
14. Make small adjustments in each iteration until the bed mesh is flat.
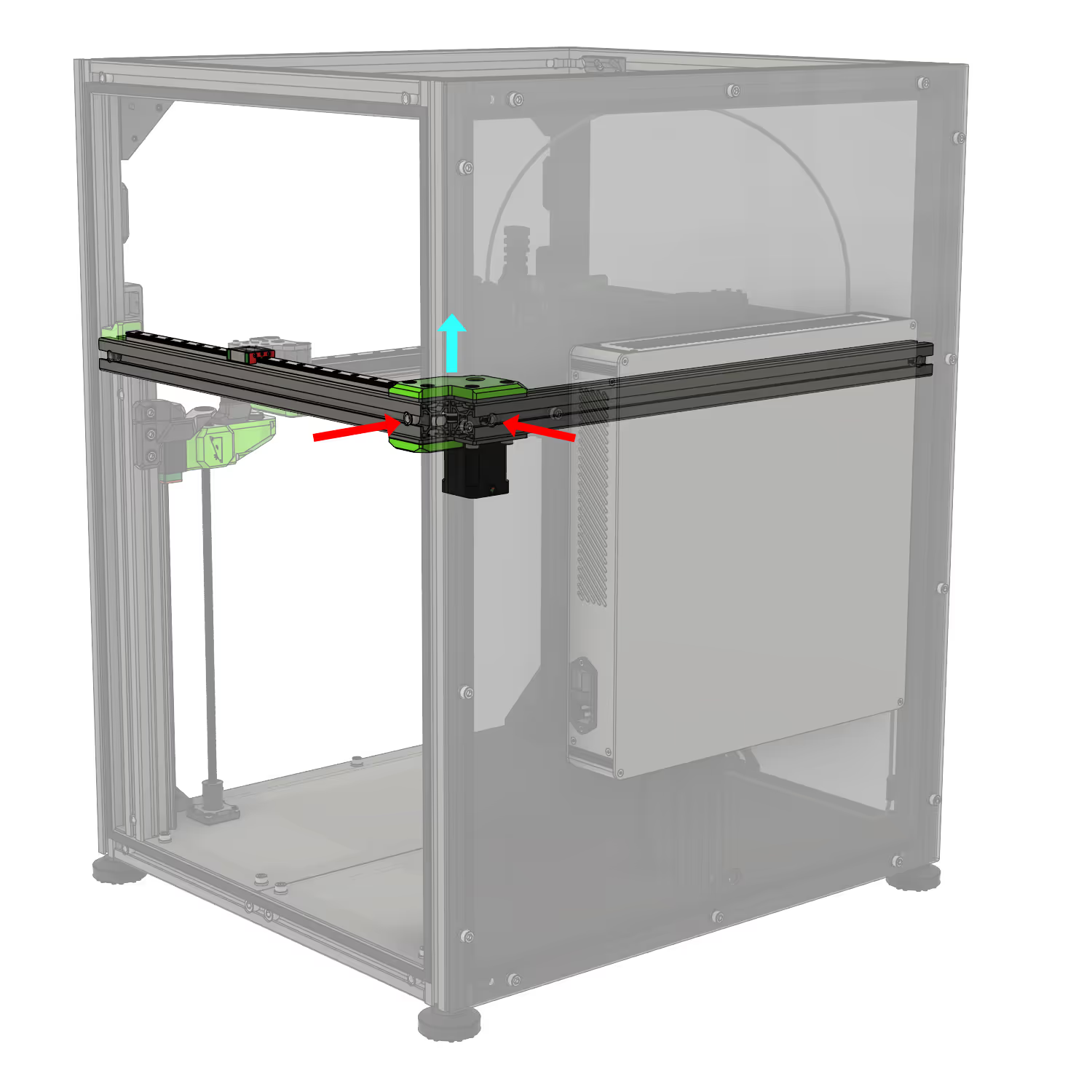
15. Unplug your machine from the electricity, turn the power off!
16. Apply the heater pad carefully, as it cannot be removed or repositioned once placed. Do not attempt to move or remove it after any part has adhered.
17. Peel back about one inch of the protective sheet from one side.
18. Align the heater pad centrally on the bottom of the aluminum bed and press down to secure the edge.
19. Gradually peel the protective sheet while adhering the heater pad to the bed. Use a flat plastic tool (e.g., an old credit card) to ensure full adhesion and remove any air bubbles.
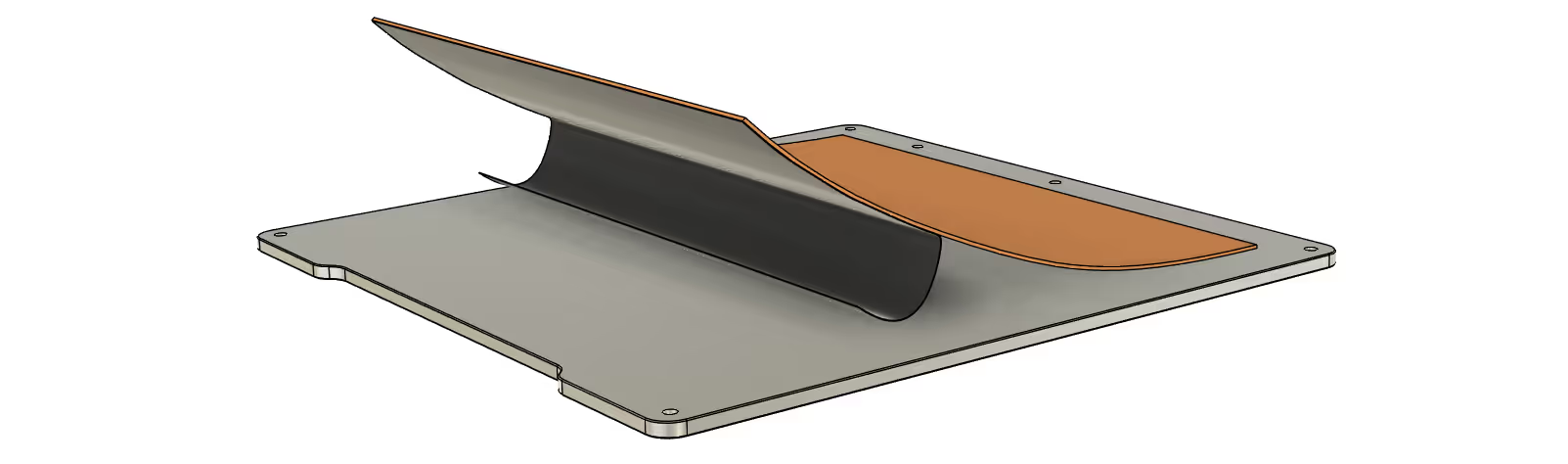
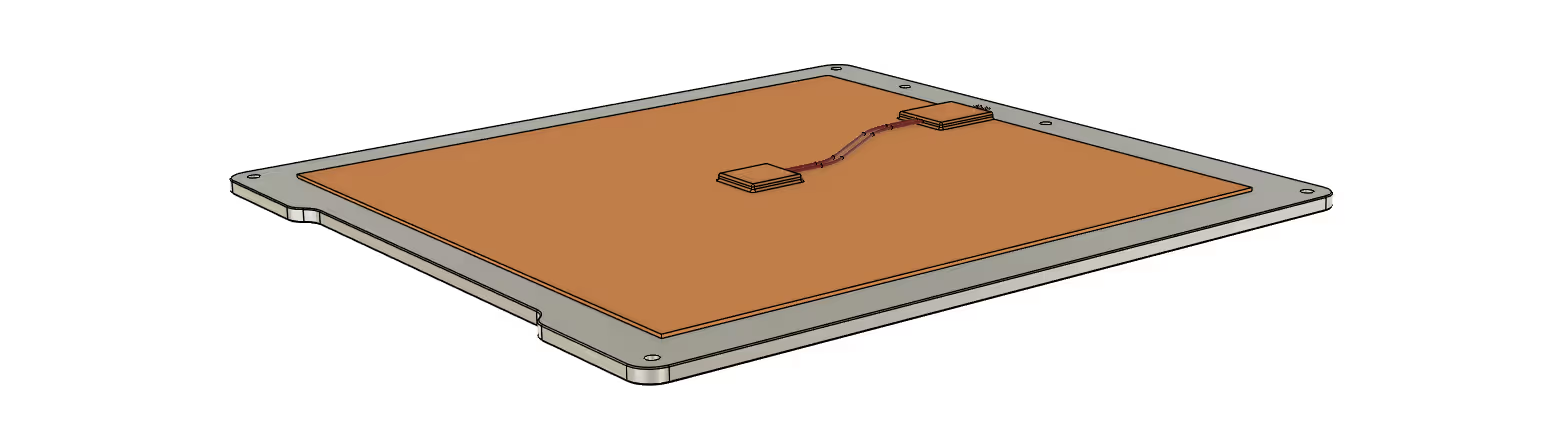
20. Using the same method, apply the magnetic surface to the top surface of the bed and install it on the V-Core 4.
21. The flexplate surface may retain impurities from manufacturing, shipping or handling, so washing it with warm water and soap is recommended before the first use. Make sure you dry it with a microfiber cloth to avoid leaving residues of whatever material you may use to dry it, regular kitchen cloths or even paper towels are not recommended.
A dirty build plate will lead to adhesion issues that might be confused with first layer squish/ Z offset calibration problems. The included textured PEI Flexplate doesn't require any type of adhesive, it’s a ready-to-print surface on its own. Regularly wipe your PEI surface down with 70-91% isopropyl alcohol to ensure any grease, or other residues, that may have accumulated on it are removed. This will help increase your surface adhesion greatly.
Bed wiring
1. After placing the bed assembly on the Z arms again, wire the bed wires as the following image shows:
Insert the bed wires through the colar on the electronics panel.
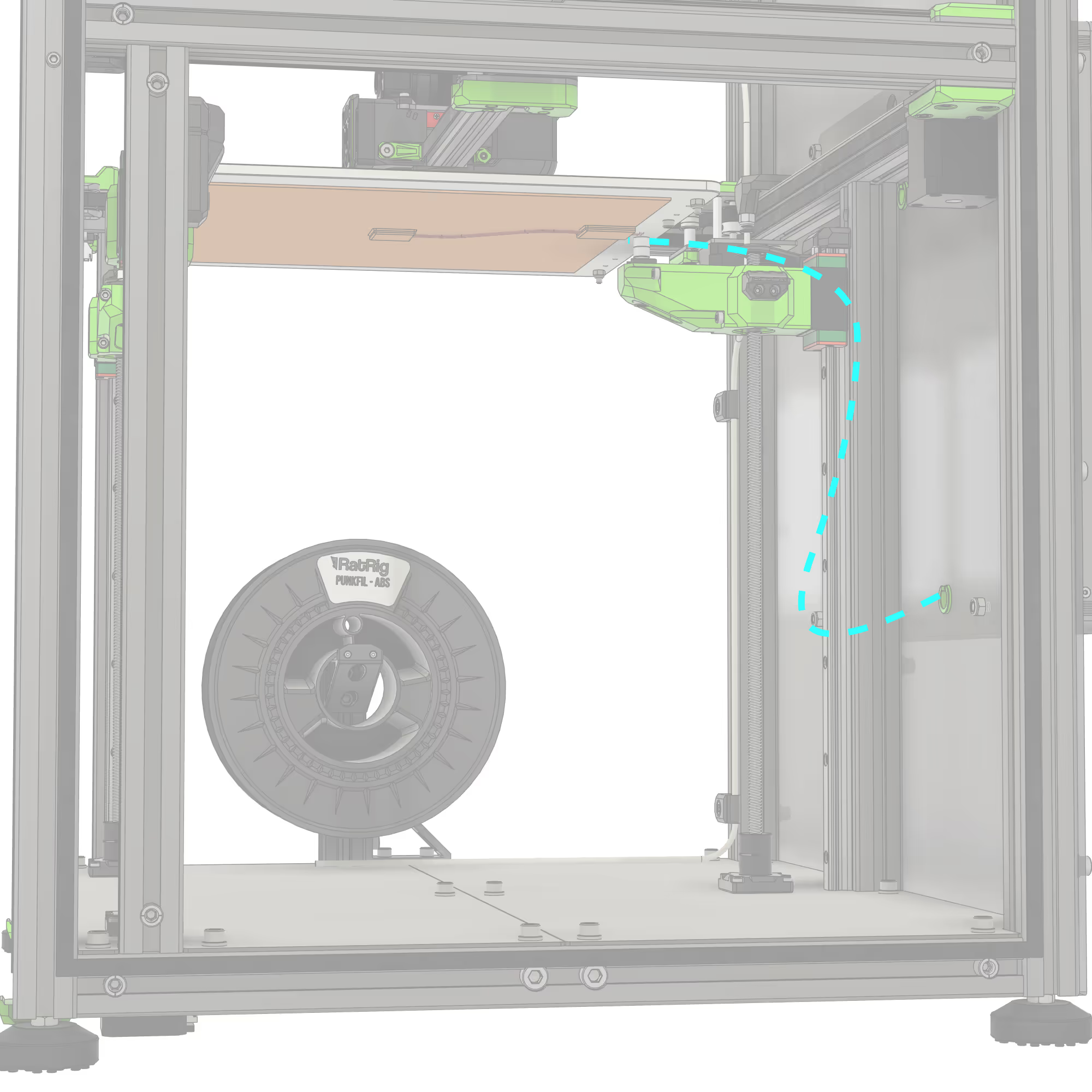
Route the bed thermistor cable as shown.
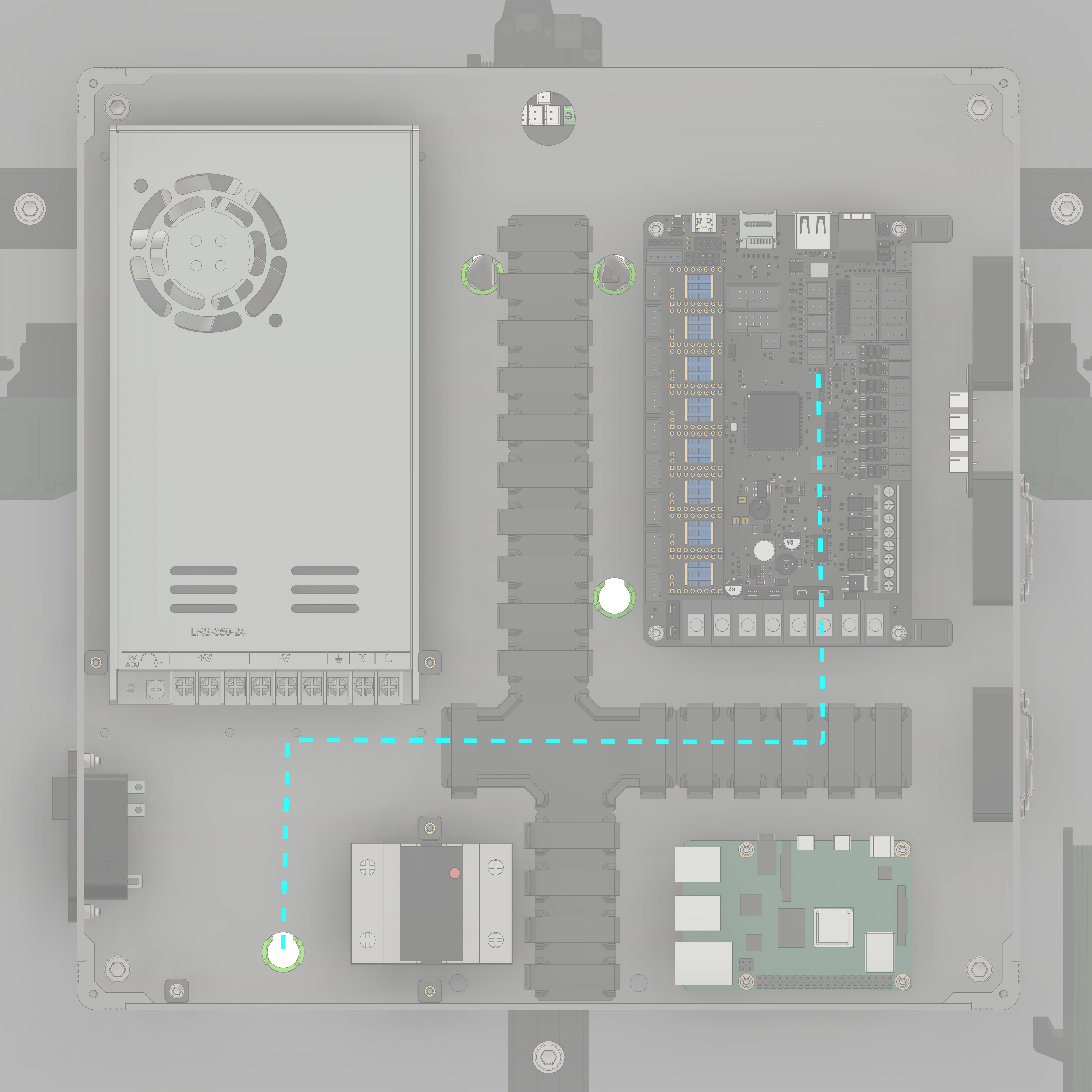
2. Complete the wiring connections for the bed heater, follow here.
3. Close the electronics enclosure using 4 M3x6mm Countersink Screws.

bed pid
PID stands for proportional integral derivative and it aims at making the heating process more efficient and consistent. Efficiency is important during heating to consume less energy, consistency is key for print quality. A badly tuned heating process looks like the graph below, where the controller can’t stabilise the temperature properly.
1. To perform a bed PID calibration, locate the "Calibration" window.
2. Click on the "PID CALIBRATE BED" button (orange square).
3. Select an average temperature at which you expect to print most often. A good starting point is 60ºC for PLA, 80ºC for PETG, and 110ºC for ABS/ASA. Click "SEND" and wait for the calibration to complete.
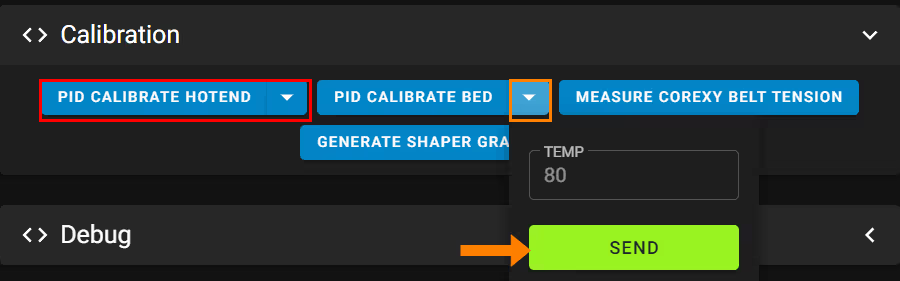
4. Once the calibration is finished, go to the console and type:
SAVE_CONFIGKlipper will restart itself with the new PID values saved to the configuration.
Hotend + fans checks (Core XY + hybrid)
1. In the "Temperatures" window. set the "Extruder" to 80ºC, and check if its thermistor reading is increasing and the 4010 hotend cooling fan is spinning.
If the hotend cooling fan doesn't turn on, you'll need to check the wiring connections and toolboard connector - more here.

2. Turn on the "Fan" at 40% to test if it is functioning properly (for more information on the 4028 fan, click here). You can find the fan control toggle under the "Miscellaneous" window in Mainsail.
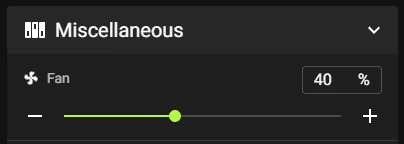
🛈 The 4028 fan is not functioning correctly. HELP
3. In the dashboard, find the calibration window. Perform a PID calibration for the hotend. Type 0 for Toolhead, then insert the temperature at wich you most expect to print at, lastly click "SEND"
We recommend: 220ºC calibration for mostly PLA prints, 240ºC calibration for mostly PETG prints and 270ºC calibration for mostly ABS or ASA prints.
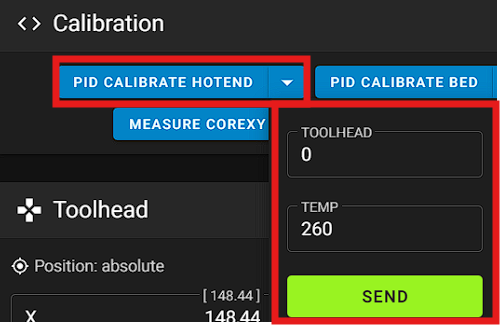
4. Once the calibration is complete, a message will appear in the console. Click "SAVE CONFIG" in the top-right corner of the screen, and the machine will reboot with the new default values.
Switch to performance mode
After validating that the machine works properly, change the configuration to performance mode. This will boost your speed and increase accuracy. Ensure the electronics enclosure fan is working (it only spins when the steppers are moving).
1. Navigate to the configurator.

2. Then to the Setup Wizard.
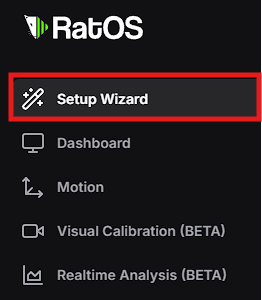
3. Select the Hardware tab
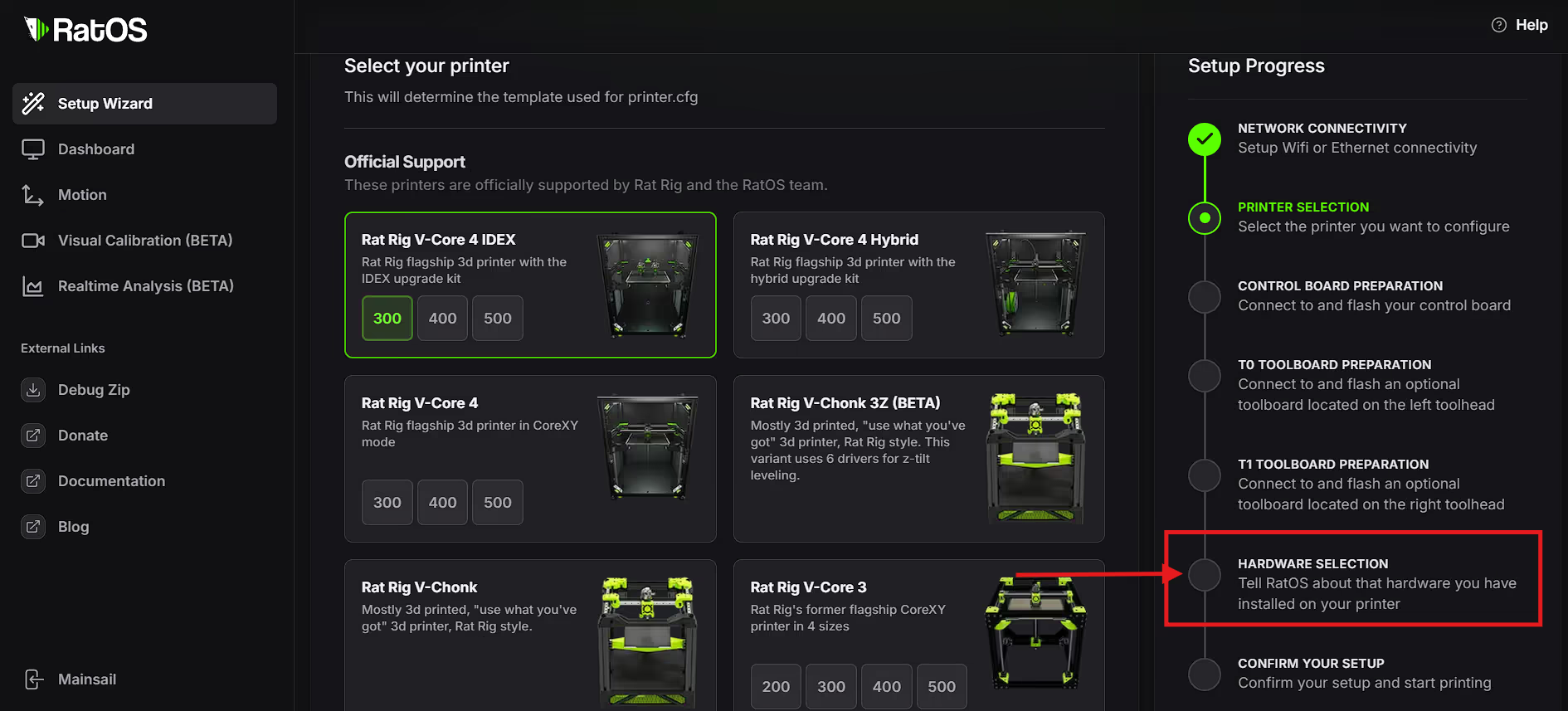
4. Scroll down and activate the performance mode.
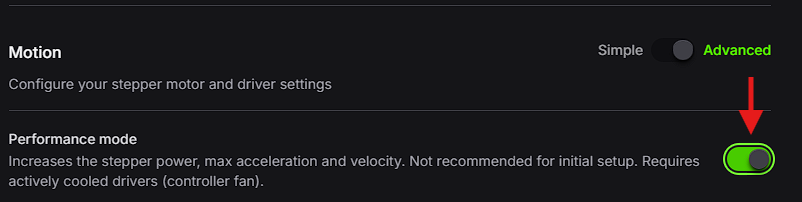
5. Scroll further down and click "Next" Then, click "Confirm And Save".
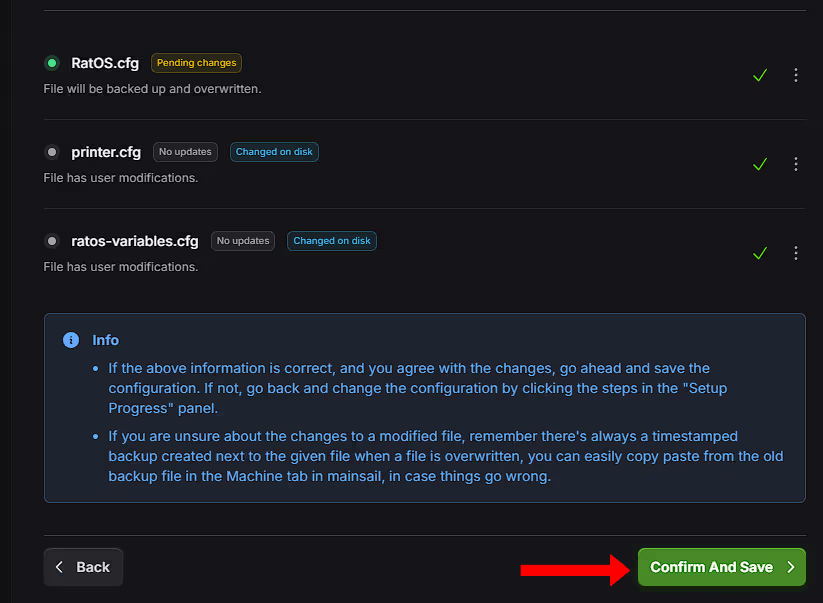
calibration
With the machine confirmed to be in optimal working condition, we can now proceed with calibration!
Click on your machine variant to show the steps to follow.
Core XY
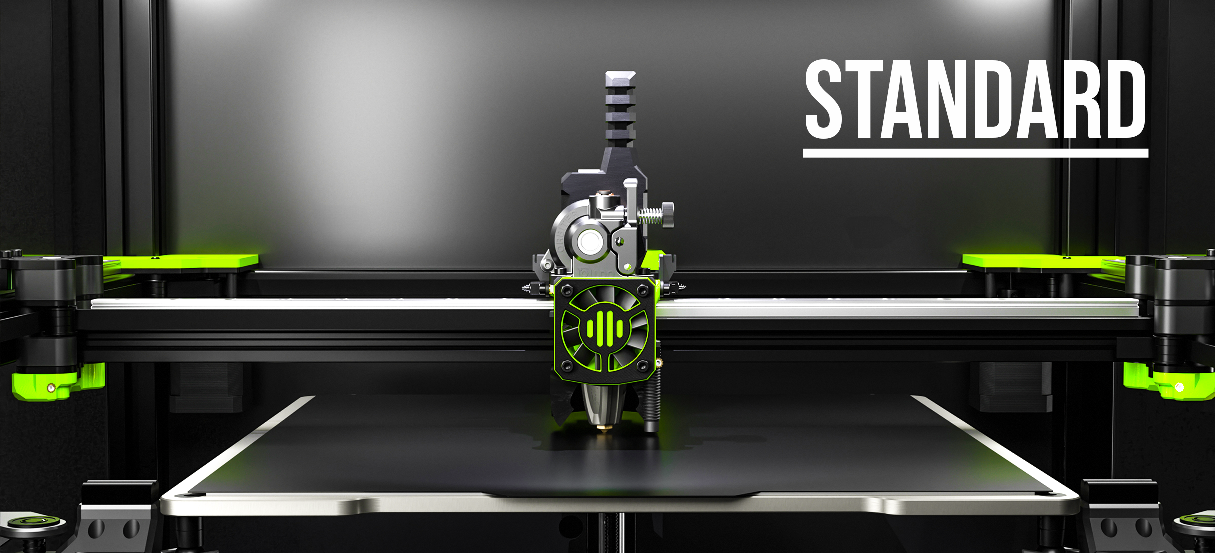
Hybrid
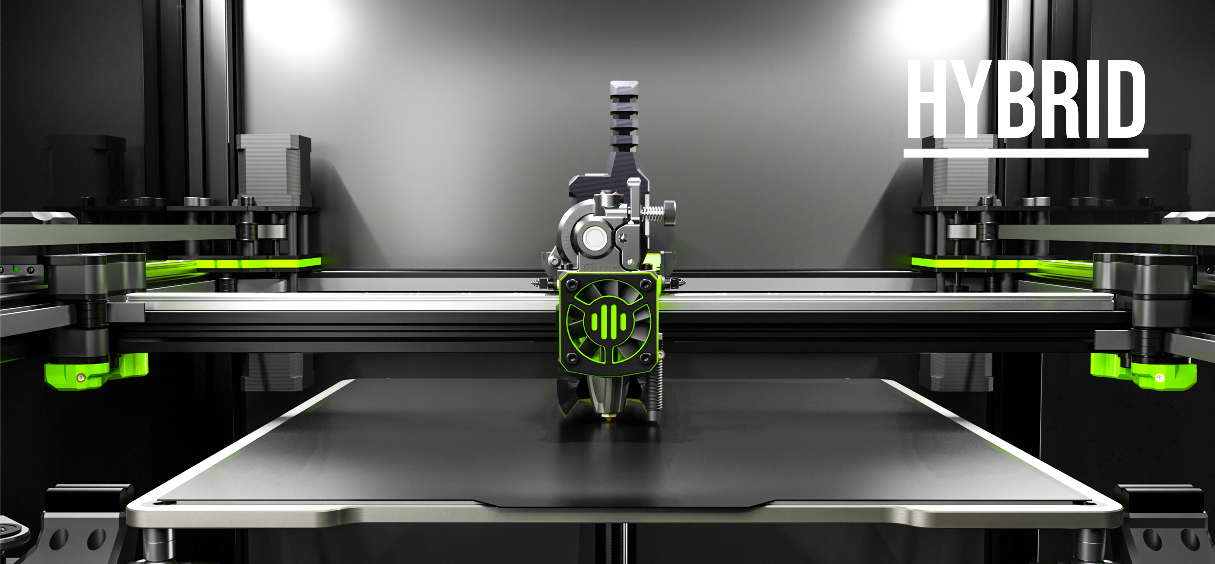
Idex
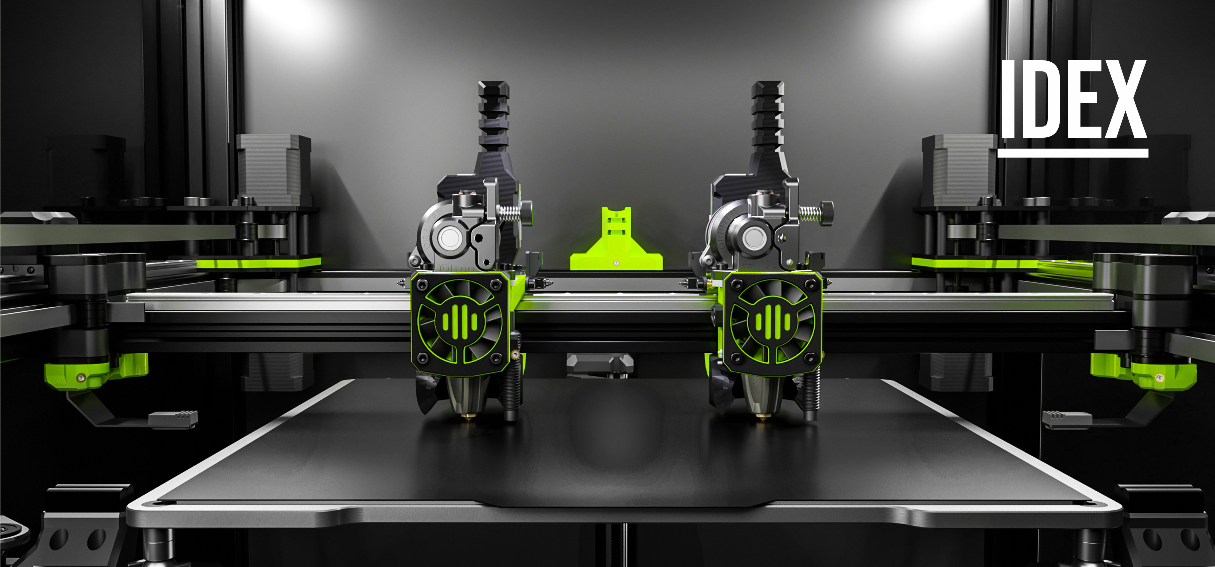
Beacon set-up
Ratos comes with a fully automated beacon model and temperature offset calibration. For further information click here.
⚠️The extruder and hot end must be clear of filament. Make sure to remove the filament; otherwise, the machine won't be able to accurately perform this calibration.⚠️
1. Heat the nozzles to 280ºC and tighten them if you didn't already. Be carefull as the hotend is very hot and you can easily burn yourself. Overtightning the nozzle can result in permanant damage. Phaetus recommends 2.5Nm of torque when hot tightening the Rapido 2 noozle.
2. Install the flex plate.
3. Run the following command:
BEACON_RATOS_CALIBRATE
🛈 ERROR - Probe sample exceed sample_tolerance HELP
Gantry twist (Core XY + hybrid)
Gantry twist significantly reduces V-Core 4 performance by introducing unwanted drag into the system. This results in poor belt tensioning and Input Shaper graphs, ultimately leading to a prolonged and frustrating process of identifying the underlying causes of the machine's suboptimal performance.
In most cases, this issue is too subtle to be detected by the naked eye. Please follow the steps below to ensure your machine is properly prepared for printing.
⚠️WARNING!
Before beginning this chapter, it is crucial to ensure that the gantry moves smoothly without the belts, and that both joiners on the gantry make contact with the stepper motor cages simultaneously. If this step is not properly completed, this chapter will not be effective. If you are uncertain, take your time to remove the belts from the machine and square the gantry as outlined in the assembly guide (check here).
1. Run the following command in your console:
M18
2. Slowly move the toolhead to the center of the machine, then slide the gantry fully to the back until the joiners make contact with the stepper motor cages.
3. Using your hands, squeeze the gantry joiners against the stepper motor cages. There should be no play between them, and the goal is to ensure you cannot squeeze the joiners further. Often, one of the joiners will be tightly compressed, while the other may have some play. Gently press both joiners against the stepper motor cages and feel for any movement. It is important to identify which joiner has play against the stepper motor cage.
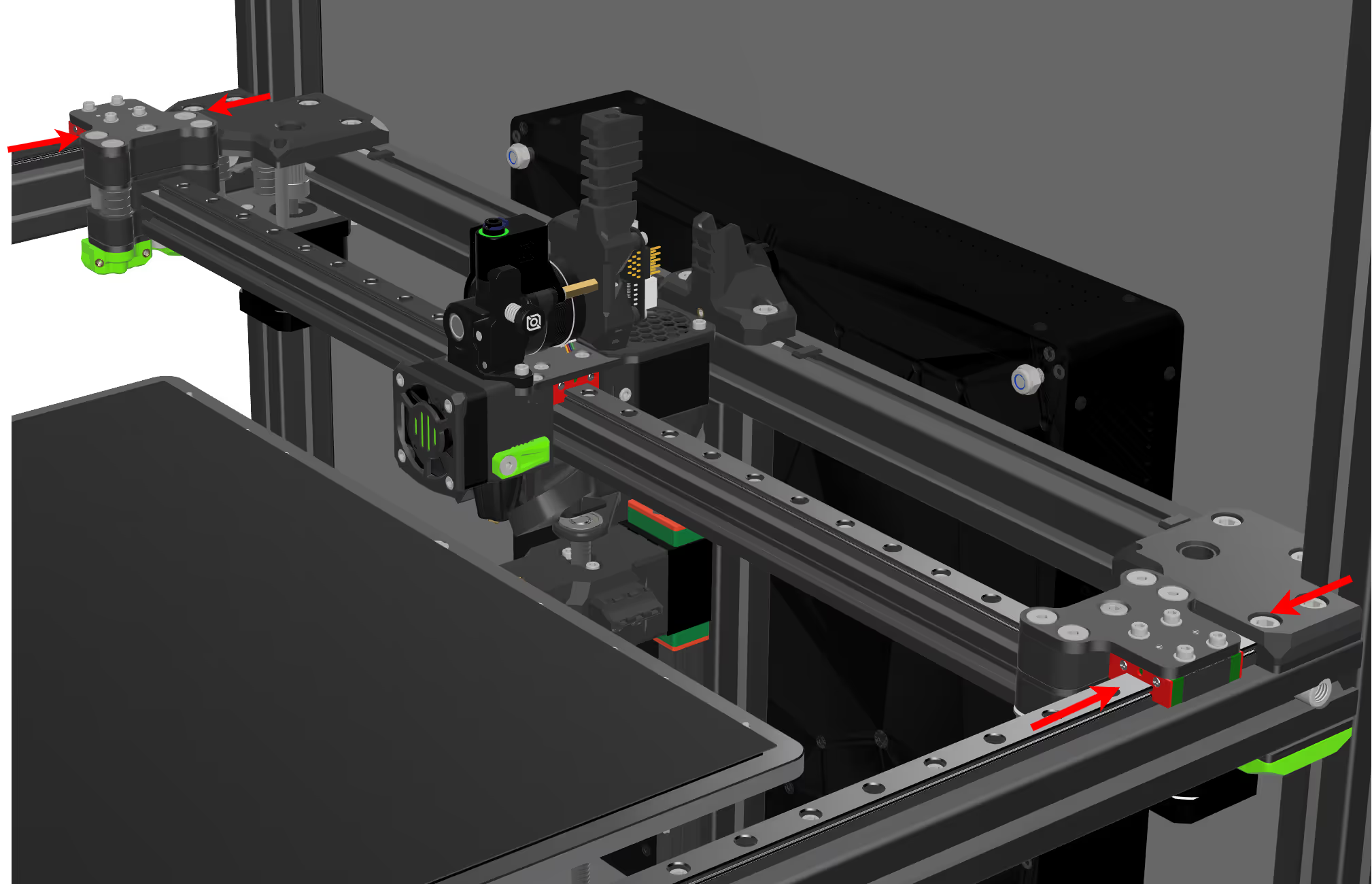
(The idlers will make contact before the plates collide, and this is perfectly fine. The idlers provide enough support and accuracy to correctly align the gantry.)
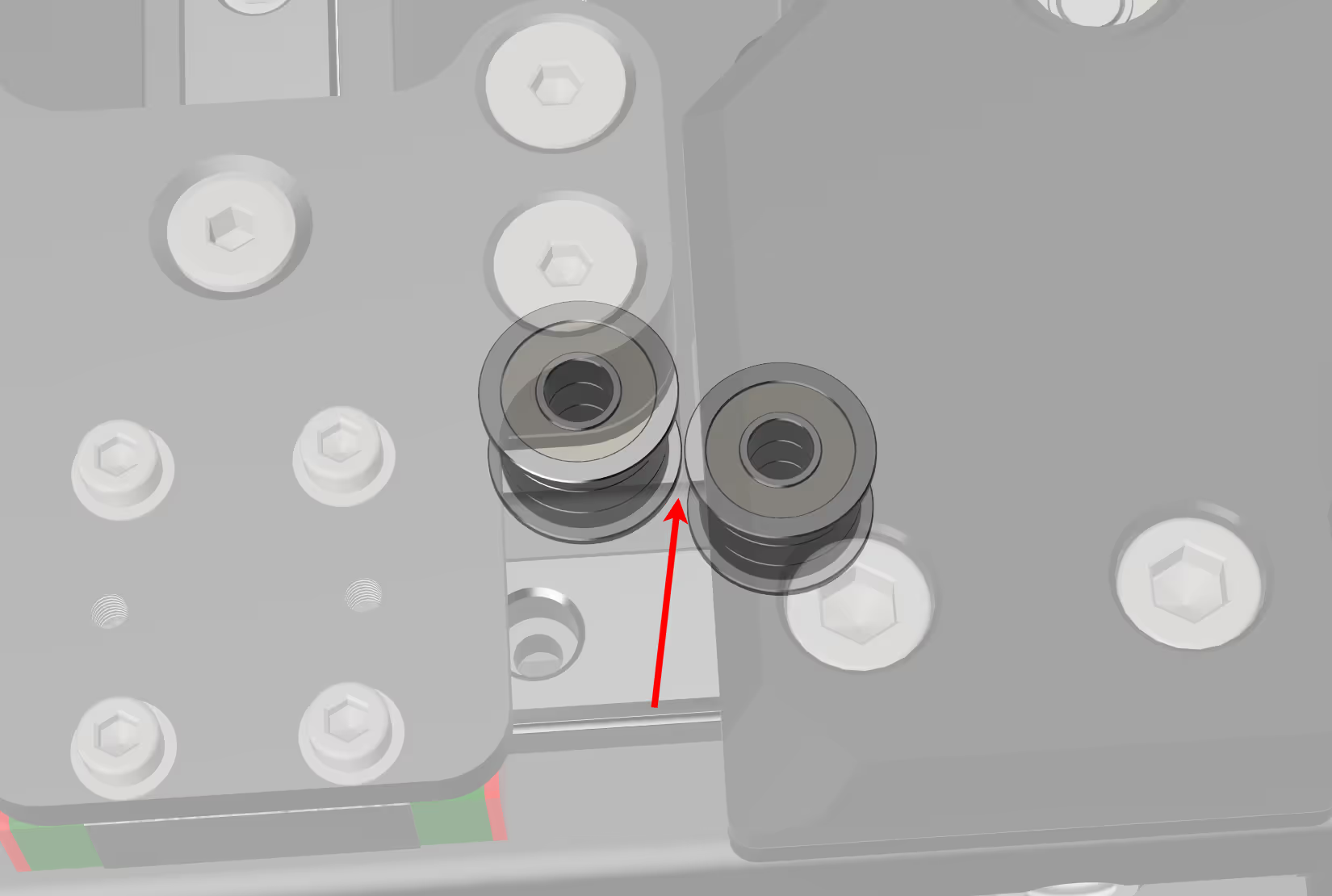
4. Identify the joiner that is not making contact with the stepper motor plate.
5. Loosen the set screw on the tensioner blocks before adjusting the belt tension.
6. Loosen the belt tensioner slightly until the joiner makes contact. Loosening the tensioner moves the joiner toward the back of the machine. Tightening the tensioner moves the joiner toward the front of the machine.
7. Make small adjustments until the joiner is properly aligned.
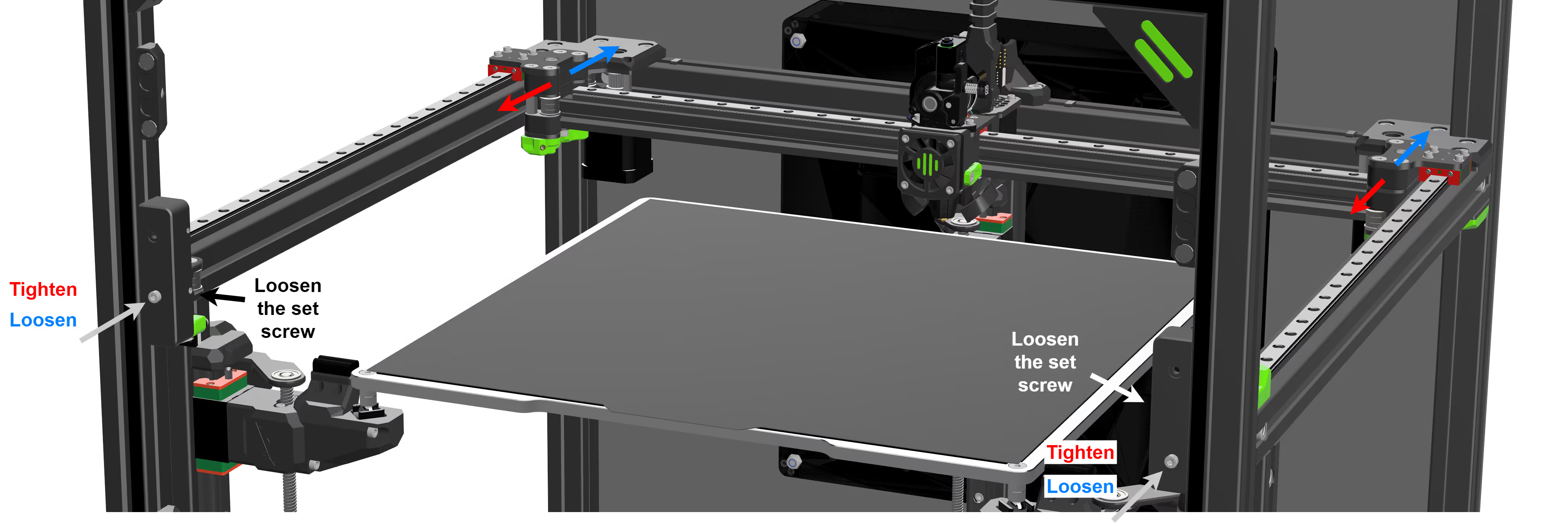
8. This calibration process involves some trial and error. Adjust the belt tension as needed to ensure that both joiners make contact with the stepper motor plates simultaneously.
9. Tighten the set screws on the tensioner body once you have finished.
Ressonance analysis
The real-time analysis tool enables real-time resonance analysis of your printer. This functionality allows you to set the printer to resonate at a specific frequency and direction, facilitating a detailed mechanical assessment. With this tool, you can more effectively diagnose potential mechanical issues within the machine. Find more detailed information about this tool here.
The following chapters will cover belt tension calibration and Input Shaper. During these stages, you can utilize the resonance analysis tool to troubleshoot and diagnose any mechanical issues with your machine.
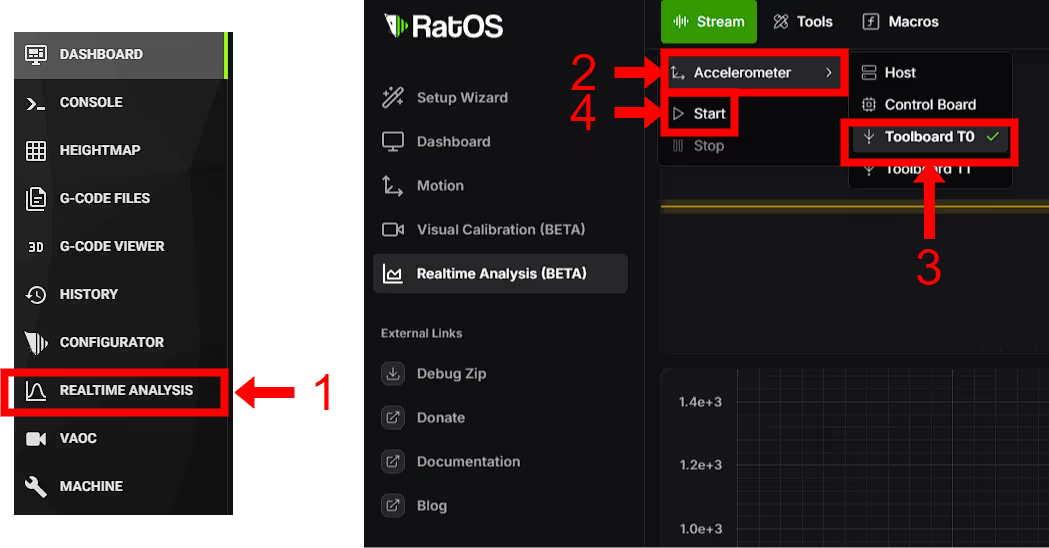
1. Click on the Real-Time Analysis button (1) in the left menu.
2. Select the Accelerometer (2).
3. If using an IDEX machine, choose the toolhead (3), either T0 or T1.
4. Click Start (4) to activate the accelerometer readings.
5. Select the resonance direction (5):
5.1 "Oscillate X" for debugging an X-axis Input Shaper spike or noise.
5.2 "Oscillate Y" for debugging an Y-axis Input Shaper spike or noise.
5.3 "Oscillate X-Y" for diagnosing resonance in the lower belt line inside the belt graph.
5.4 "Oscillate X+Y" for analyzing resonance in the top belt line inside the belt graph.
6. Choose the Oscillation Frequency (6) at which you want the machine to resonate.
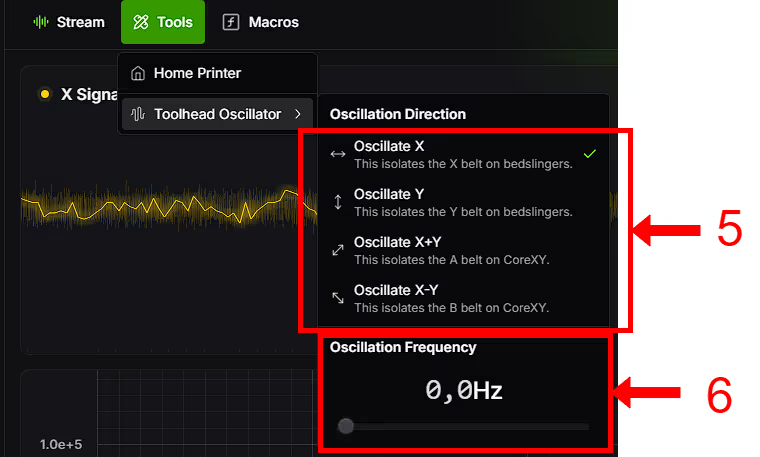
Belt tension
Please note:
- This section details the relative belt tensioning on the CoreXY and Hybrid variants only. For Hybrid variants, this procedure is simplified by performing it without the Y belts installed. Reinstalling the Y belts for Hybrid is covered later in the guide.
- If you are building an IDEX, you have already reinstalled the Y belts in step 10 (Gantry Twist). The IDEX toolheads can only be moved by the printer when the Y belts are installed, so the graph-based belt tensioning procedure can only be performed with them installed. This complicates the procedure, ###AND A SPECIFIC GUIDE IS NOT YET PROVIDED###. If in doubt, skip the belt tension section.
The belt tension graphs are meant to help you troubleshoot your machine assembly, do not look at it as a tunning tool, it's very easy to over-obsess with them. It's impossible to cover every scenario and diagnose every belt graph artefact, this is a very complex and sensitive subject, about which we are still exploring and learning, please feel free to submit your feedback in our Discord community.
Also check out the amazing work by the klippain shaketune team here!
Ensure your machine build is finished, all the wirings are clean and there are no loose parts, the machine must be placed on a sturdy surface and there is nothing on top or against the machine. Don't touch the machine during vibration analysis.
It's important to clarify this procedure focused on relative belt tension, meaning it will show you if both belts have the same tension. This is crucial for a smooth motion system.
Ideally, the belt graph for a V-Core 4 would have smooth lines with 2 peaks, as shown below:
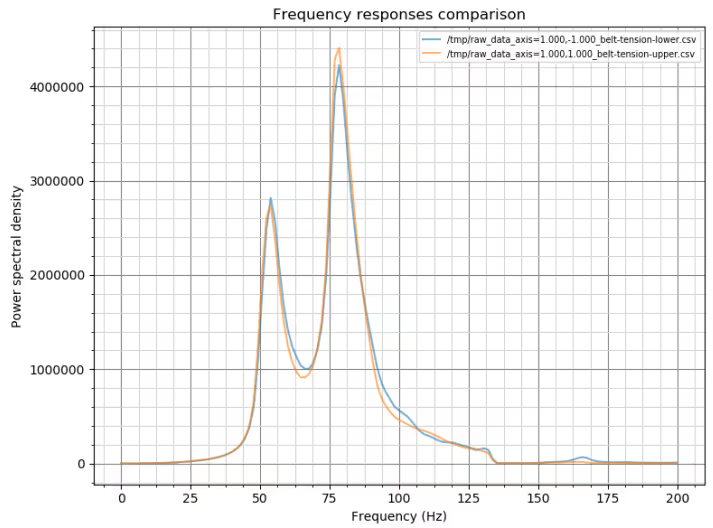
1. To perform a belt tensions graph, just click on the designated button inside the "SCRIPTS" window.
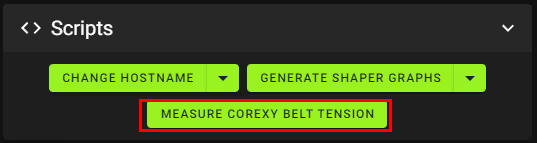
2. You must now analyse your graph and identify potential issues. This is a very complex and involved process, but here are a few generic most found issues.
2.1) The two peaks (blue and orange) must be aligned on the same frequency, if they are not vertically aligned, then you need to tension or loosen the belts, and your gantry is most likely twisted. Refer to this guide to help you troubleshoot
2.2) Toolhead vibrations generally cause vibrations on the lines around 100-150 Hz. This can be caused by loose screws, damaged printed parts, loose wires, lack of zip ties to properly constrain the wires, etc...
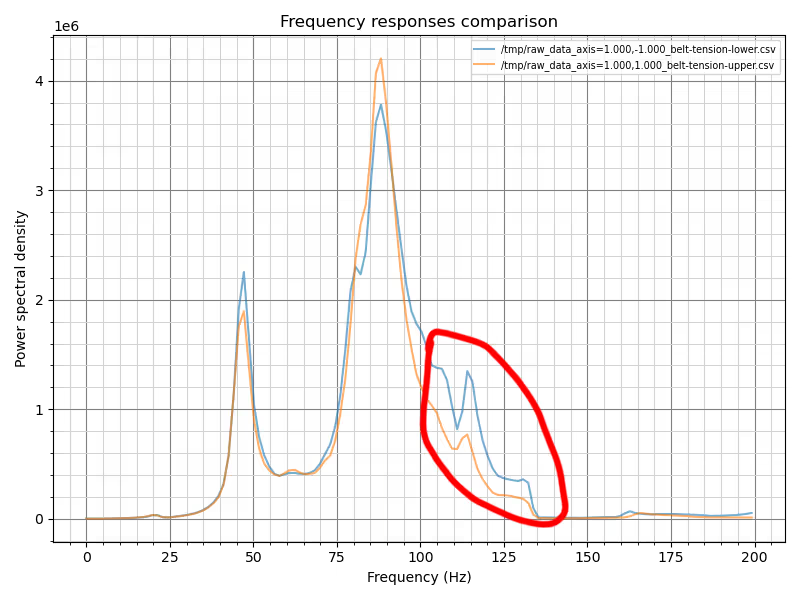
3) There is an issue with the belt path- If your graph lacks one or two peaks. this most likely indicates your belts are rubbing against something somewhere on their path, this can be an Idler, Motor pulley, frame, etc...
Only one belt path is having issues on this example:
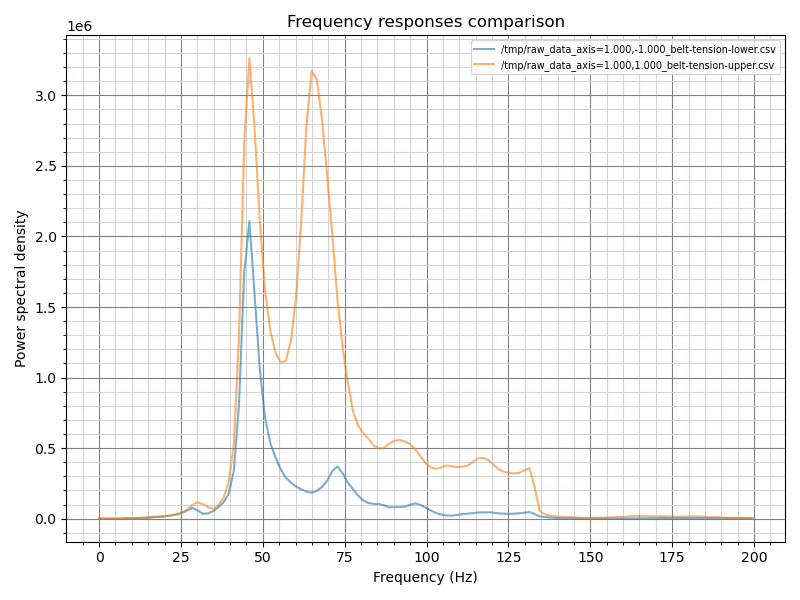
3.1) Both belts path have issues in this example:
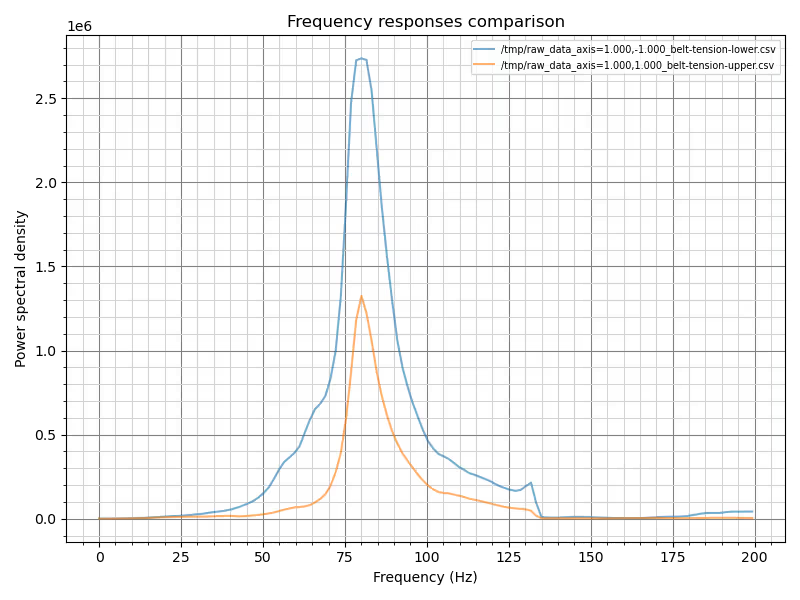
4) Lastly, it's important to differentiate between vibrations and swinging.
Vibrations manifest in zig zag alike lines and are mostly caused by loose screws on the toolhead or the gantry. Loose idler stacks or missing shims can cause the same effect. try to locate them and fix the issue.
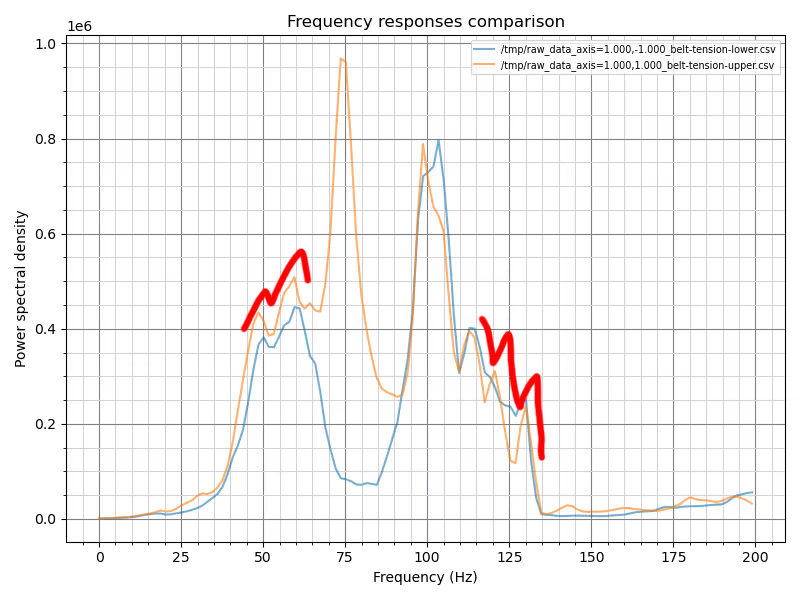
5) Swinging does show as smooth curves. Many times it's coming from the fact that the printer sits on a shaky table or an uneven floor. Make sure your printer can't shake.
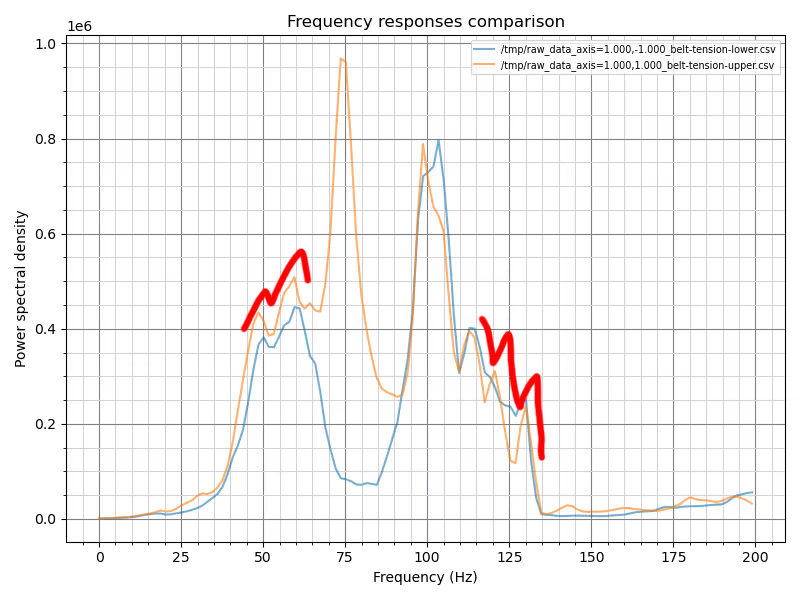
Input ShapER (IS) (CoreXY+Hybrid)
This calibration follows the Klipper documentation steps but they are simplified for the V-Core 4.
1. Click on the designated button "GENERATE SHAPER GRAPHS" inside the "SCRIPTS" window.
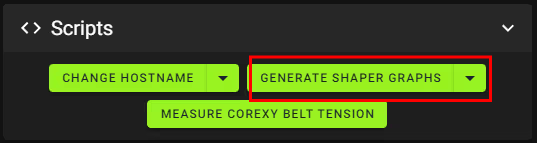
The printer will start moving the gantry in X and Y to determine the ringing frequencies. After this, the input shaper graphs will be available under the “machine” tab (1) , inside the “input_shaper” folder (2).
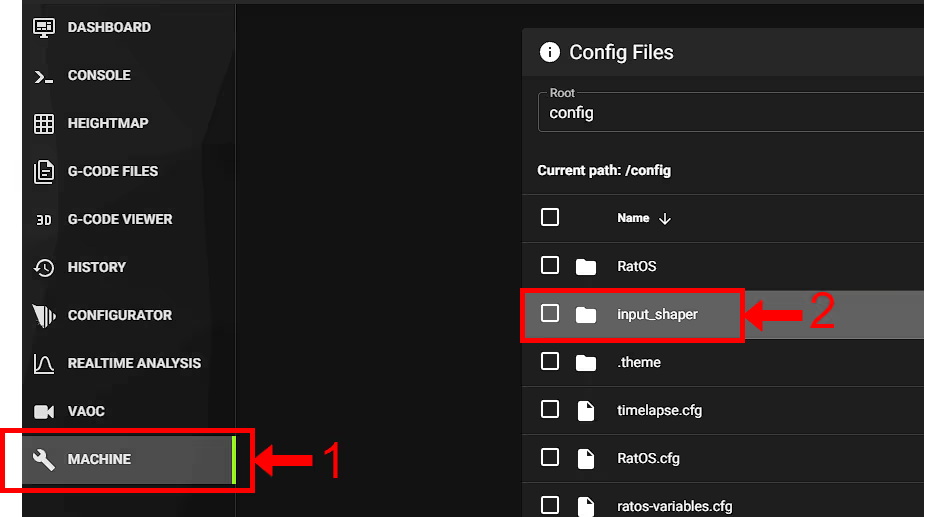
2. Look at the generated IS graphs, you should have one for the X-axis and one for the Y-axis. The example below highlights the relevant details to look for in an IS graph.
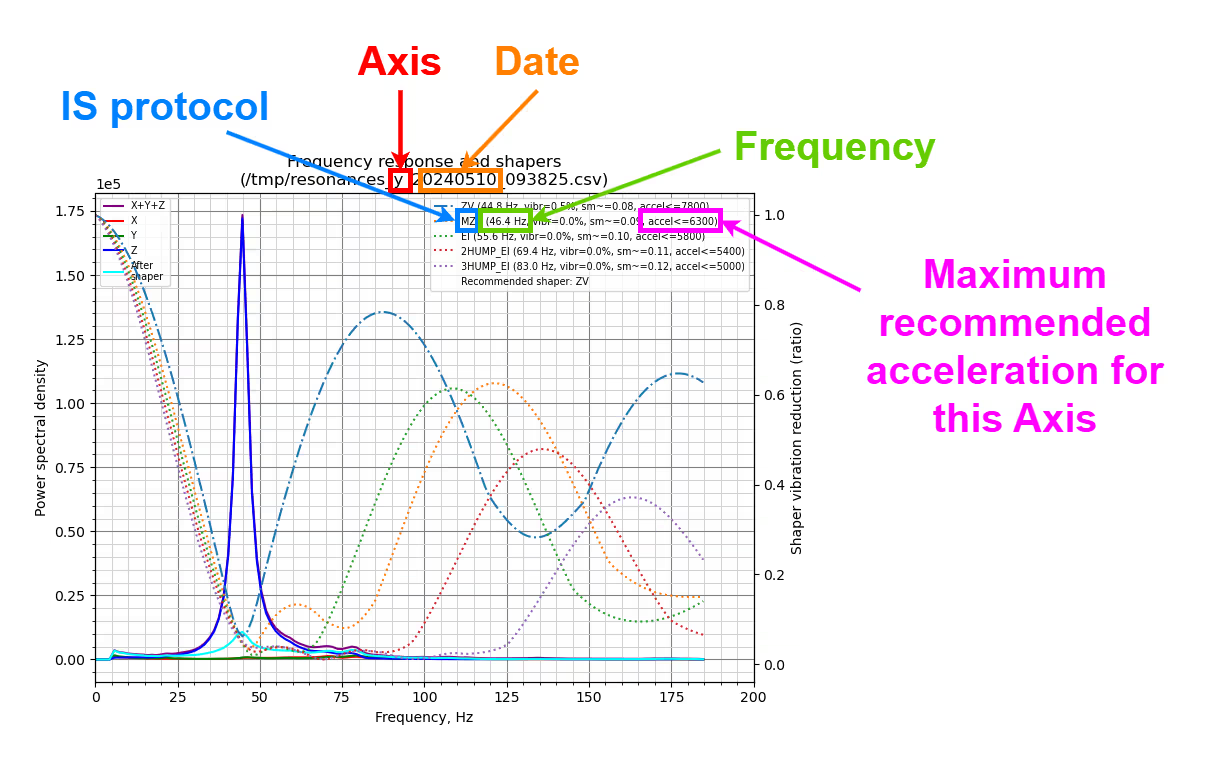
MZV (46.4 Hz, vibr:0.0%, sm~=0.09, accel<=6300)
Notice that this protocol recommends a max acceleration of 6300 mm/s2. You will need to compare this value with the one provided on the X graph and choose the lowest value, this value should be used as your external perimeter acceleration inside the slicer profile, to avoid having any visible ghosting. The external perimeter speed and acceleration on the V-Core 4 profiles are somewhat conservative, you can increase them based on your input shaper results to achieve the maximum quality VS performance.
3. Inside the “printer.cfg” go to “user overrides” and paste the following lines:
[input_shaper]
shaper_freq_x: Your_X_Frequency
shaper_type_x: mzv
shaper_freq_y: Your_Y_Frequency
shaper_type_y: mzv
4. Click "SAVE & RESTART" at the top right of the print.cfg page.
Skew Calibration
Skew correction is meant to compensate for a 3D printer assembly which is not perfectly square, the software makes small changes to the toolhead movement, maintaining a perfectly square trajectory. Every detail during the frame assembly may cause a slightly twisted frame, even the screws tightness. Making sure the machine is as square as one can get by hand is very important before advancing to software skew calibration.
The V-Core 4 has a 3-point kinematic bed levelling system that helps to mask XZ and YZ skew problems. If the build was successful and all Z rails are properly aligned, the Z squareness shouldn’t be a problem, otherwise, a skew calibration should be done for all planes. In this guide we’ll only focus on the XY plane, the procedure is the same for the other axis, more information here.
1. Start by downloading the Skew_correction_tool.stl. Then open it inside your slicer. If this is your first time following this guide, please follow the Slicer installation first, then get back to this step.
🛈 When slicing the model, make sure the A corner is pointing to the origin of the plane.
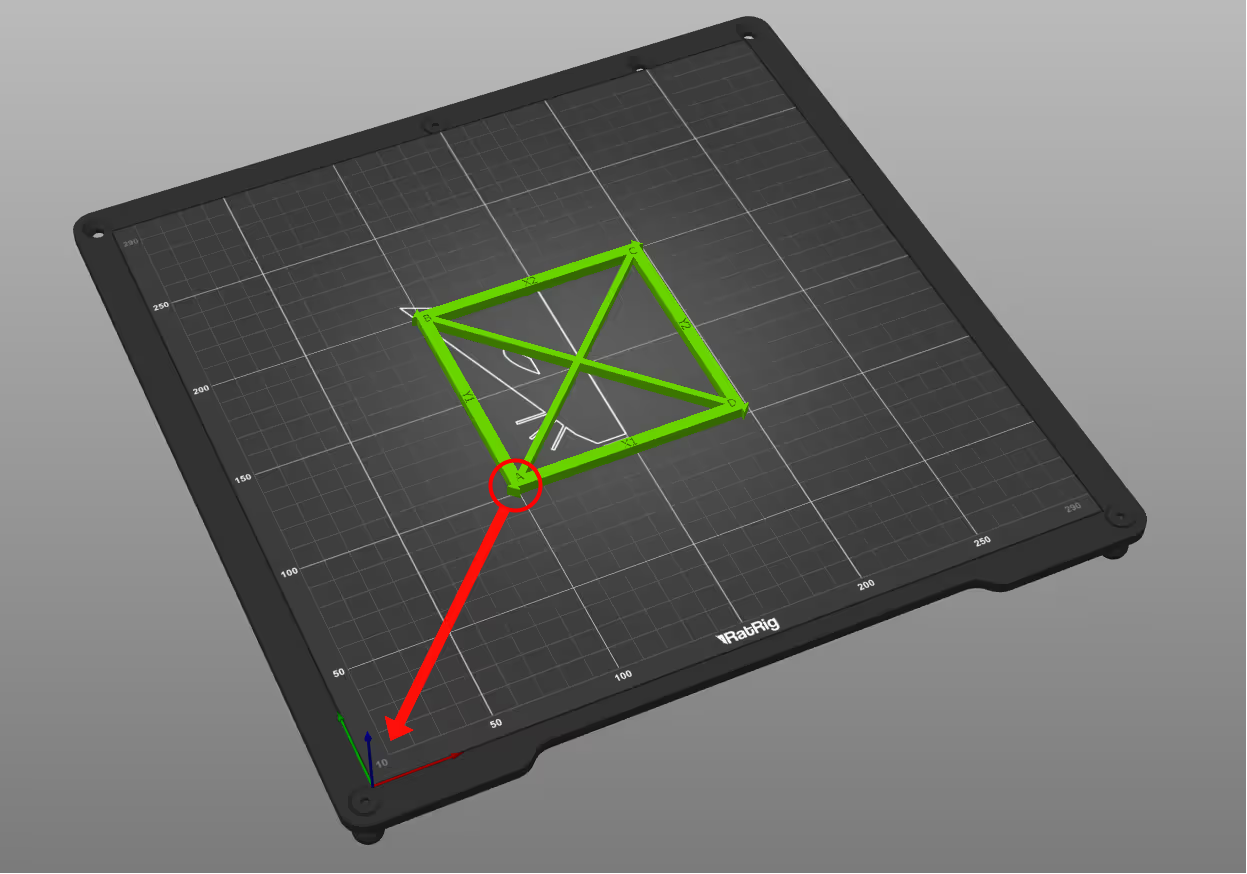
2. Guarantee that no skew correction is running on your machine, check that variable_skew_profile is commented out in the macro configuration section. or type the command below in the terminal. For more information, click here.
SET_SKEW CLEAR=1
The [skew_correcton] module requires 3 measurements; the length from Corner A to Corner C, the length from Corner B to Corner D, and the length from Corner A to Corner D.
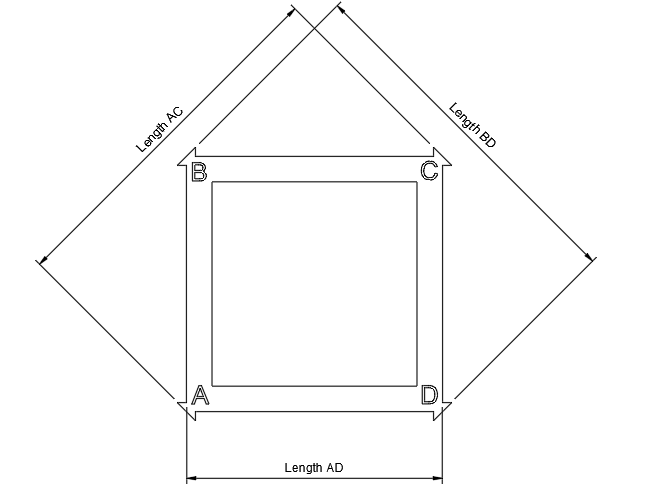
Let's take the following measurements as an example:
AC= 141.15mm
BD= 140.9mm
AD= 99.65mm
3. Go into the printer.cfg and add the following lines:
[gcode_macro RatOS]
variable_skew_profile: "my_skew"
4. Click “save and restart” at the top right of the printer.cfg window, then paste into the console:
⚠️Replace the BOLD text with your values.⚠️
SET_SKEW XY=AC,BD,AD
With the previous example, we have:
SET_SKEW XY=141.15,140.9,99.65
Followed by:
SKEW_PROFILE SAVE="my_skew"
5. Type:
SAVE_CONFIGand re-print the test, make sure AC=BD. If not, double check all measurements and start this calibration again.
6. IDEX ONLY If you are commissioning an Idex V-Core 4, you will need to performe the Initial VAOC calibration again, click here.
⚠️ Select the IDEX machine variant at the begining of the "calibration" chapter to show the IDEX specific chapters ⚠️
Operation and Slicer
Click on your machine variant to show the steps to follow.
Core XY
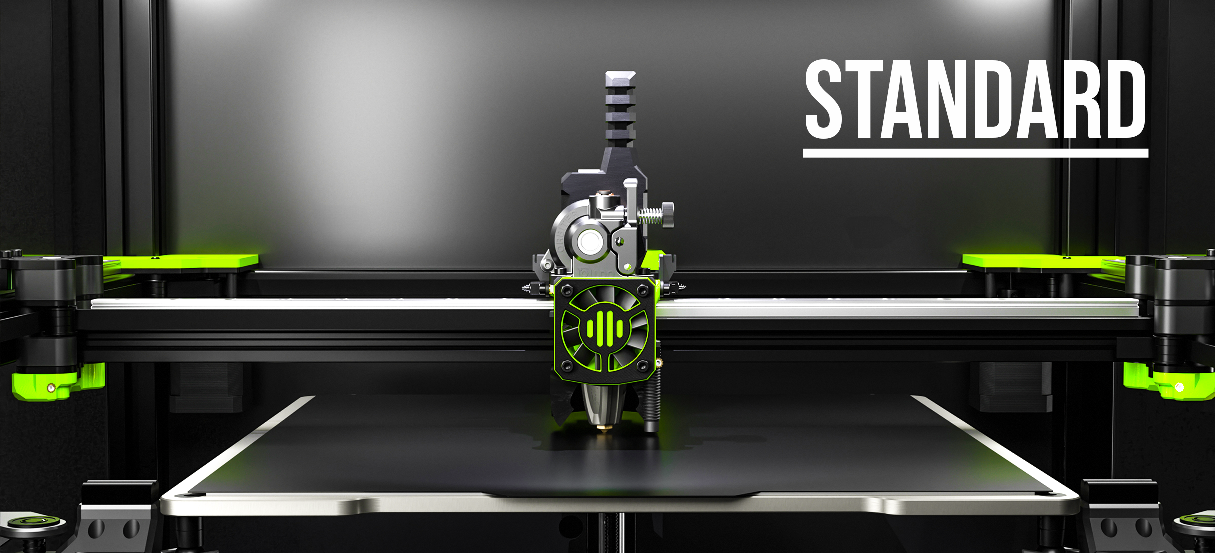
Hybrid
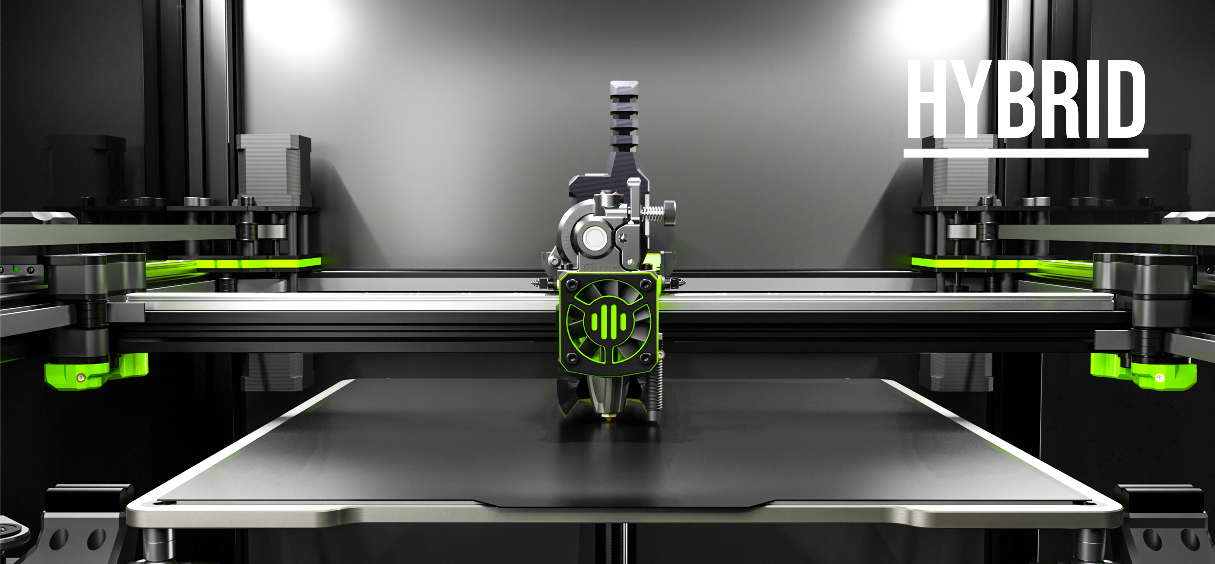
Idex
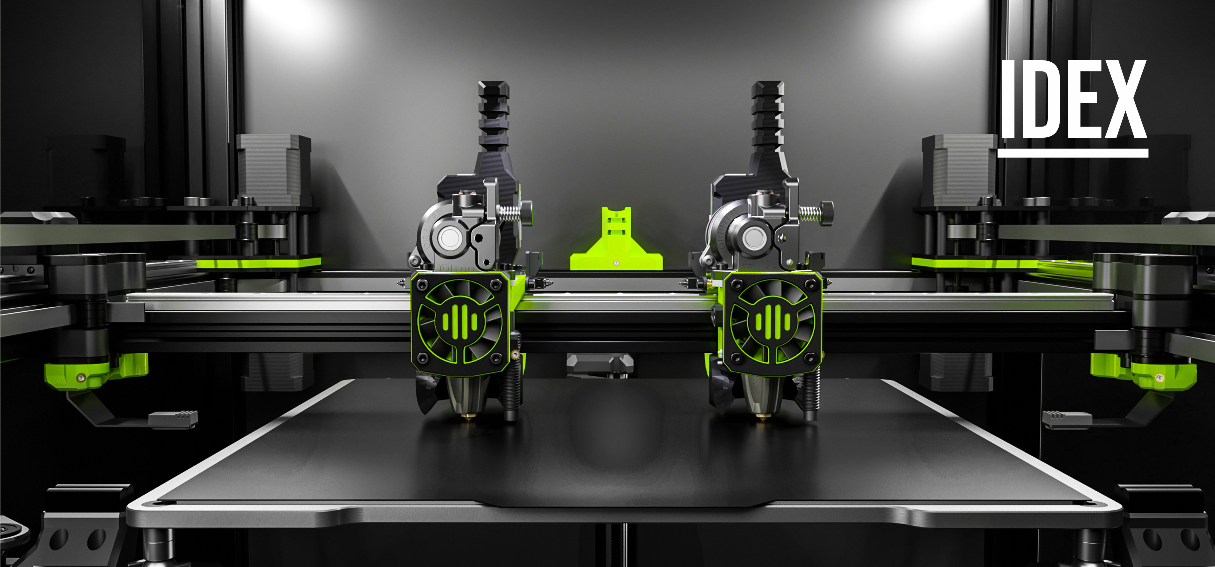
obtaining a slicer
There are many Slicers free to download, RatRig recommends that you use one of these three, as they have the biggest communities.
Recommended - Prusa Slicer is a free and open-source project. It can be obtained here.
SuperSlicer is a free and open-source project. It can be obtained directly from their GitHub repository.
OrcaSlicer is a free and open-source project. It can be obtained directly from their GitHub repository.
A Slicer takes 3D models (STL, OBJ, 3MF) and converts them into G-code instructions for 3D printers.All Rat Rig profiles available on these slicers are meant to help you get printing as fast as possible, they are not fully tuned profiles to extract the full potential of the V-Core 4, they are a solid platform to build upon!
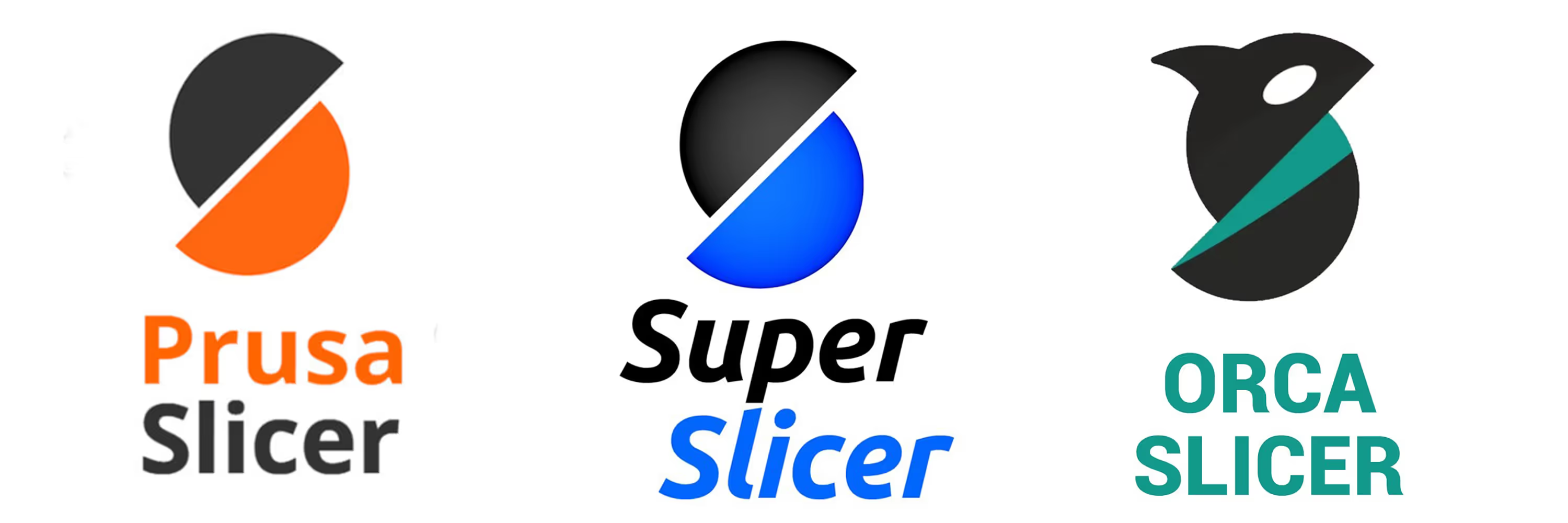
slicer configuration
Simply choose the appropriate V-Core 4 profile for your machine variant and size. In Prusa Slicer the V-Core 4 is under "other vendors" > "RatRig", In SuperSlicer and OrcaSlicer is under "RatRig".
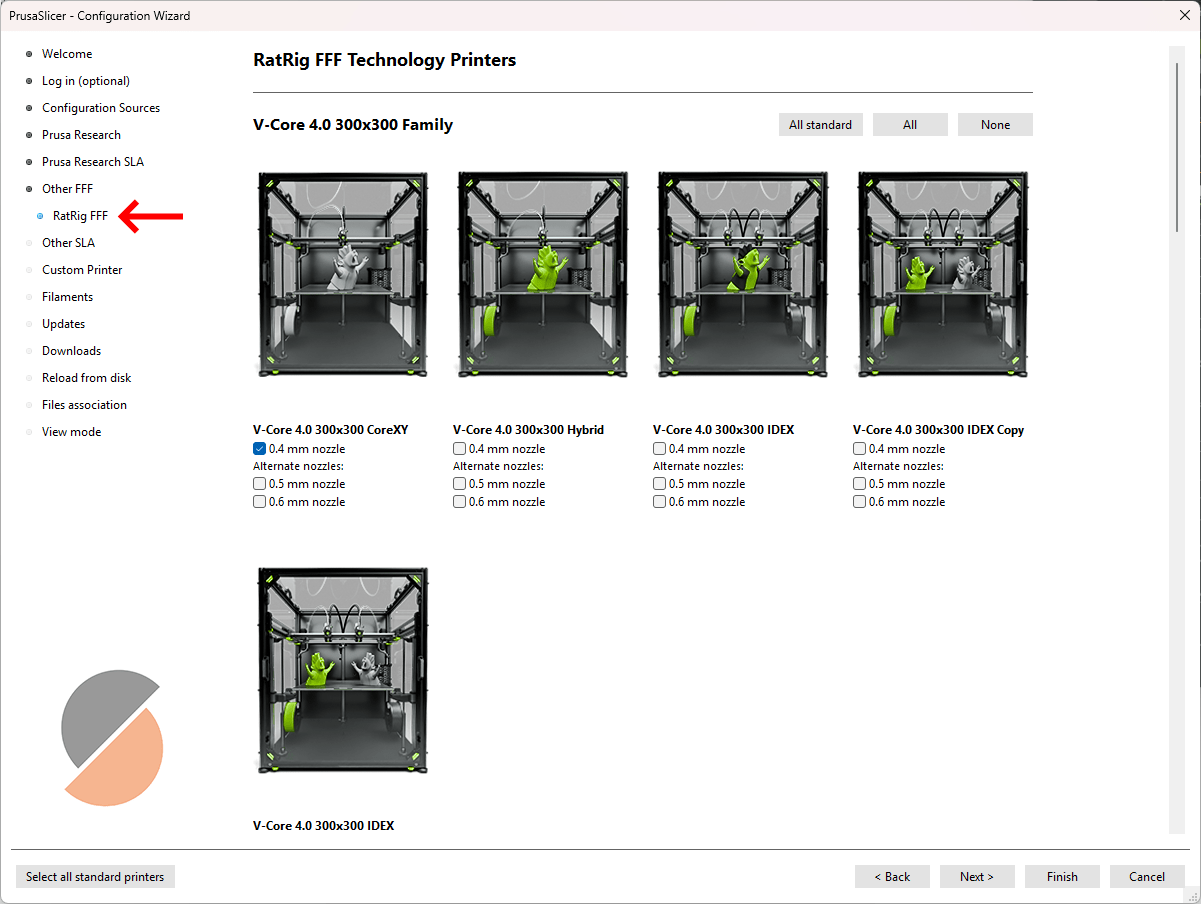
You can also add filament profiles, RatRig has included pre-tuned Punkfil profiles! Even if you are not using our filament, we recommend using the profiles for the same types of materials, as many factors like cooling, extrusion multiplier, and pressure advance are pre-tuned for you, they won't work as well for different brands but it's a solid starting ground:
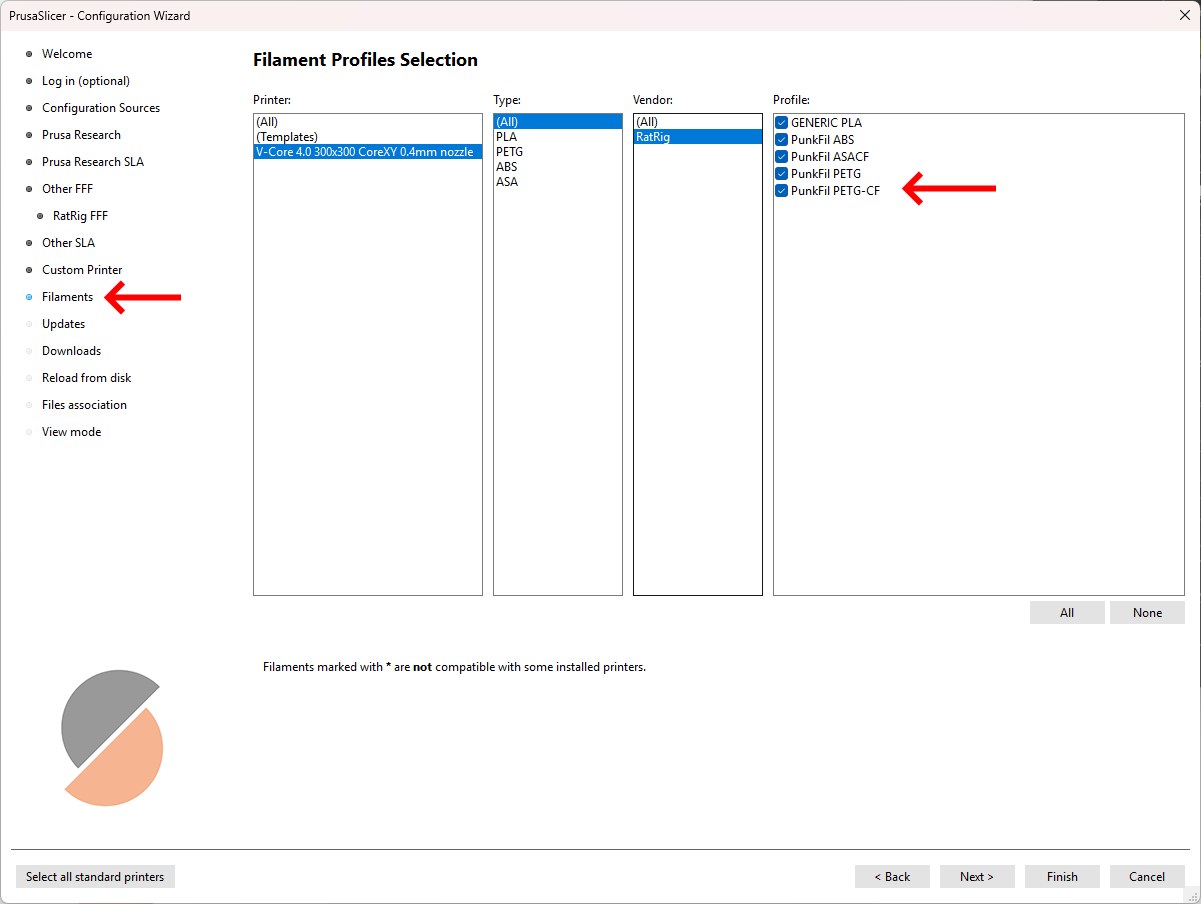
Add your machine (Optional)
You can connect your machine directly to the slicer, allowing for a smoother workflow by sending the print job directly from the slicer software.
1) Select your machine and click on the gear next to it.
2) Click "add physical printer"
3) Define a machine name
4) Select "Klipper (via moonraker)" and insert your machine url, created during the RatOS configuration.
5) Click "Test" to ensure your machine is connected to the Slicer, you should see a "Sucess!" window, otherwise check if your machine is connected to the same wifi network as your computer.
6) Click "OK".

how to slice
Rat Rig provides predefined slicer parameters for all V-Core 4 models, which will produce optimal results in most cases. However, due to the inherent variability of 3D printing, certain parts with complex geometries may require adjustments to slicer settings to achieve the best print quality.
1. Open PrusaSlicer and import the selected STL file by dragging it into the slicer (1).
2. Next, select the print settings (2), which define parameters such as part strength, surface finish, resolution, and other relevant factors.
3. Choose the filament type (3), which sets material-specific parameters such as printing temperature and cooling power.
4. Select the machine size, variant, and nozzle size (4). Finally, click "Slice Now" (5) to generate the print file.
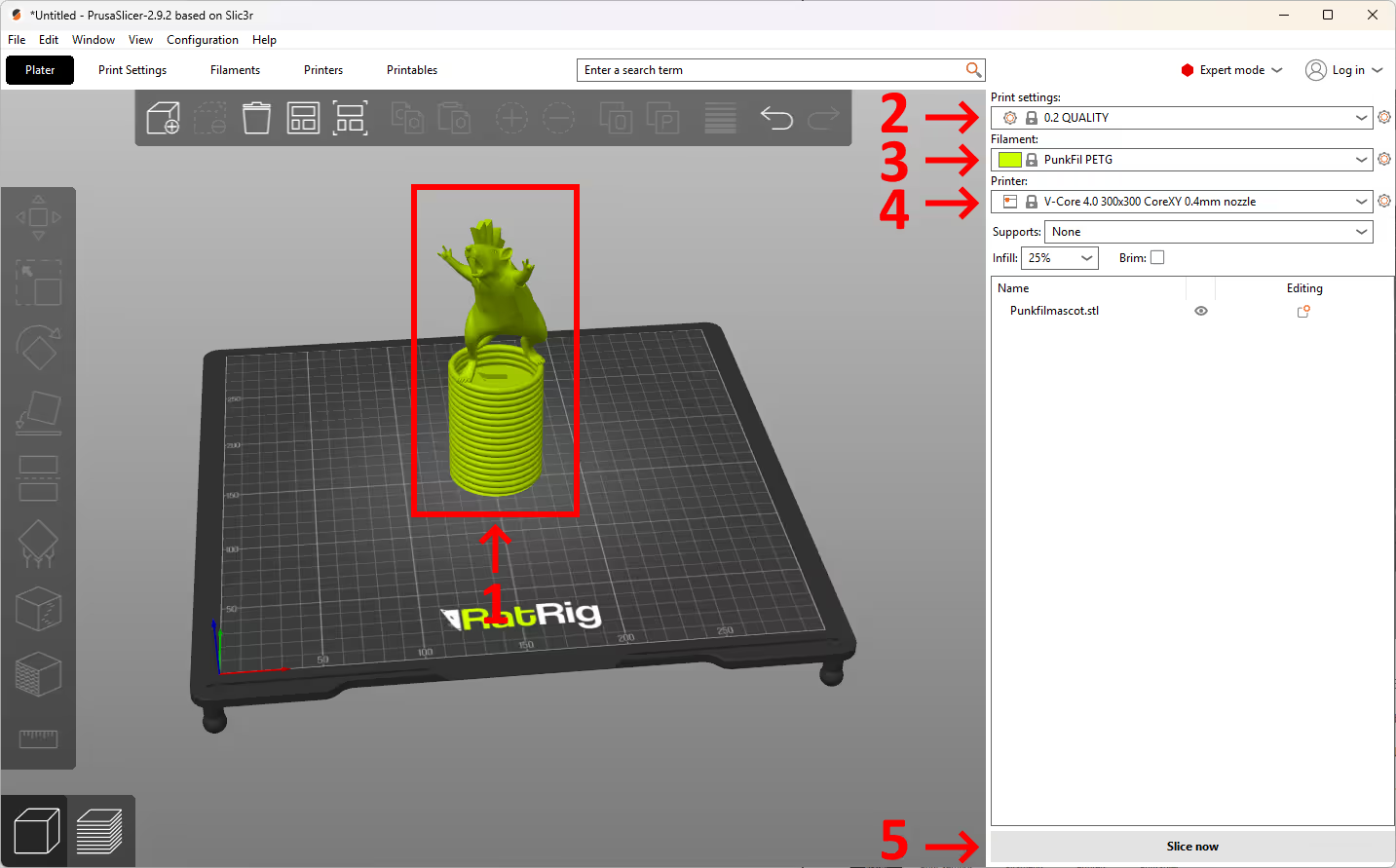
5. After slicing, the slicer will generate a layer-by-layer preview of the printed part. You can use the vertical toggle (6) to inspect each layer individually.
This feature helps identify potential geometry constraints that may need adjustments in the print settings. Simply drag the toggle up and down to review the layers. While this step is not required for printing, it is a useful habit as you become more familiar with slicer settings. Once satisfied, click "Export G-code" (7) to generate the print file. Then, upload it to Mainsail, and you're ready to start printing!
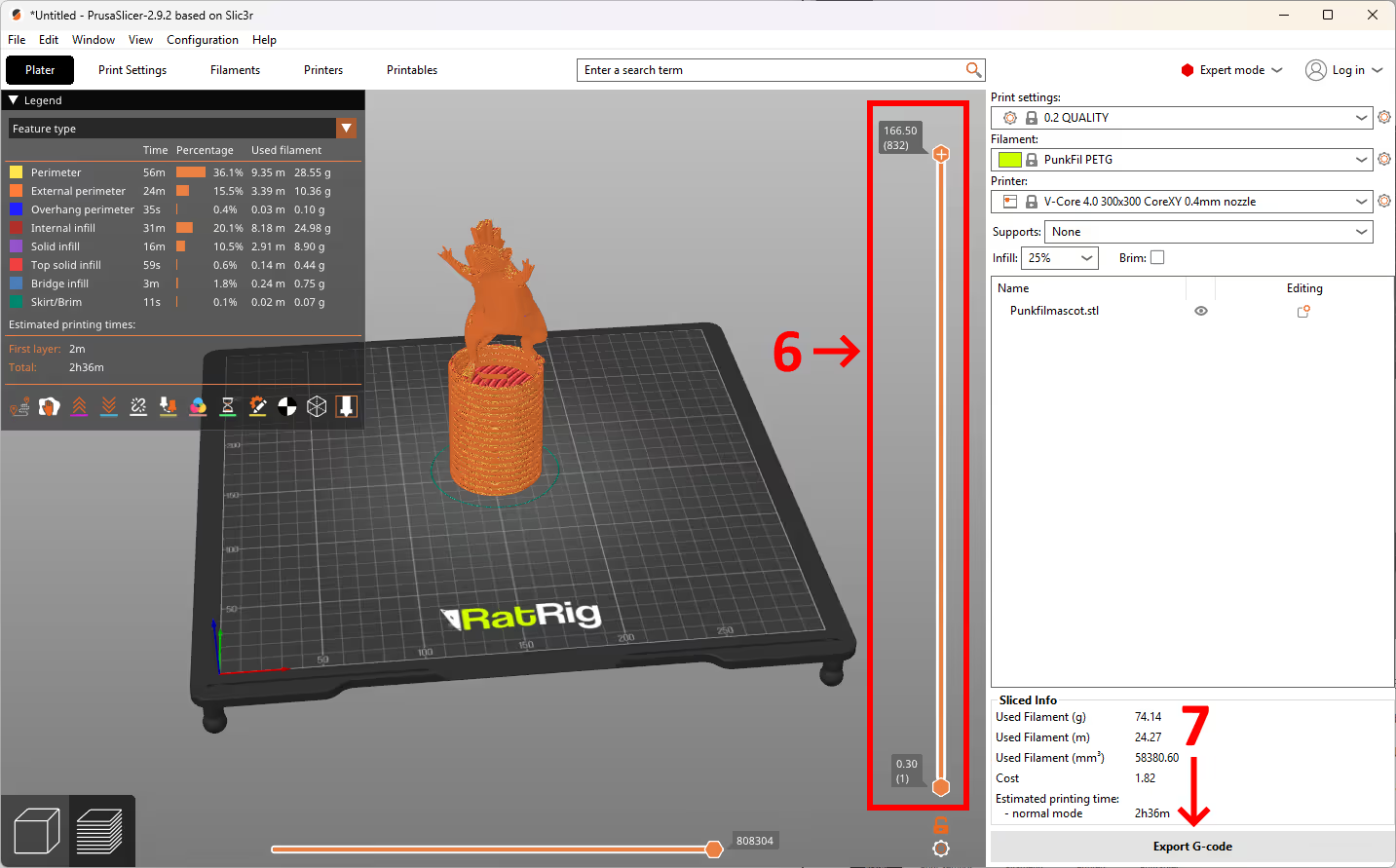
After finishing this guide you can print our Punkfil Mascot to see how your machine is performing, this is all the tuning you need to get started with very good results. Further tuning might be required to achieve a specific goal, other settings not approached here are not essential and can worsen the print quality if not done correctly.
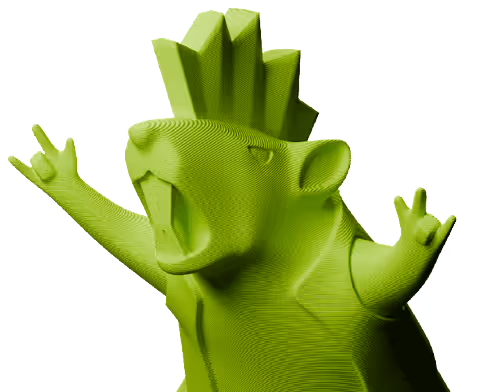
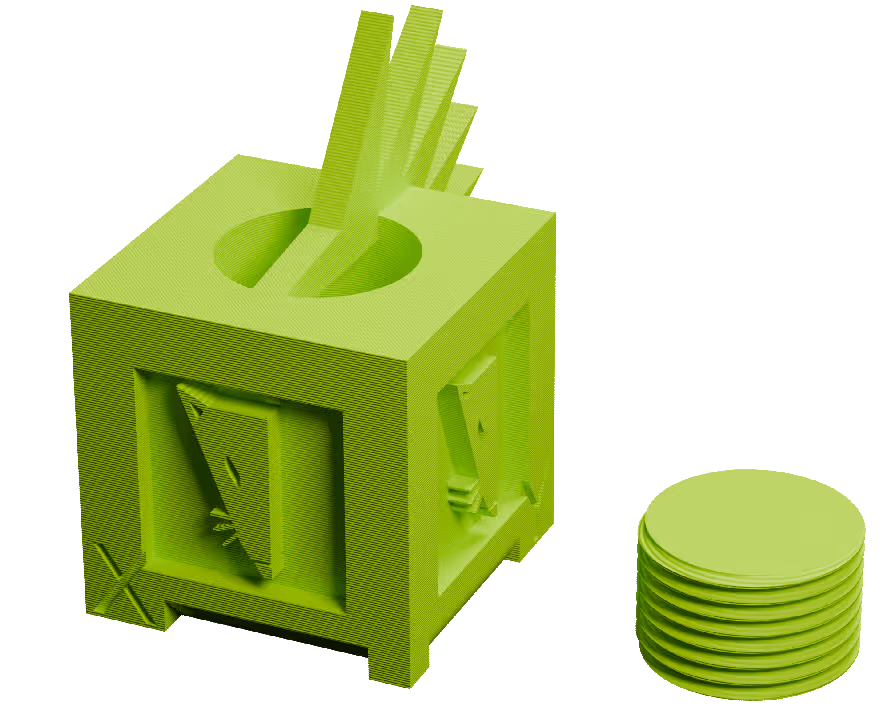